Flachglas hat an seinen drei Standorten in Deutschland kontinuierlich in neue Technologien investiert. Auf diesem Weg hat der langjährige Partner Glaston die Modernisierungsinitiativen des Unternehmens aktiv unterstützt und Anlagen geliefert.
Bei der jüngsten Optimierung lag der Schwerpunkt auf einer alten Laminieranlage, die seit den 1970er Jahren ein Eckpfeiler des Betriebs ist. Ziel war es, sie mit der ProL-Technologie von Glaston zu modernisieren, um Effizienz- und Nachhaltigkeitsstandards zu erfüllen und gleichzeitig ihre einzigartigen Fähigkeiten zu erhalten.
In nur 15 Tagen wieder voll einsatzfähig
Flachglas brauchte viel Mut, um Änderungen an dieser Linie vorzunehmen. Im Laufe der Jahre hat das Unternehmen auf dieser Linie eine große Anzahl von Spezialglas-Produkten entwickelt, die ein beträchtliches Fachwissen erfordern. Flachglas wollte sicherstellen, dass die Qualität dieser Spezialprodukte nach der Umstellung nicht beeinträchtigt wird.
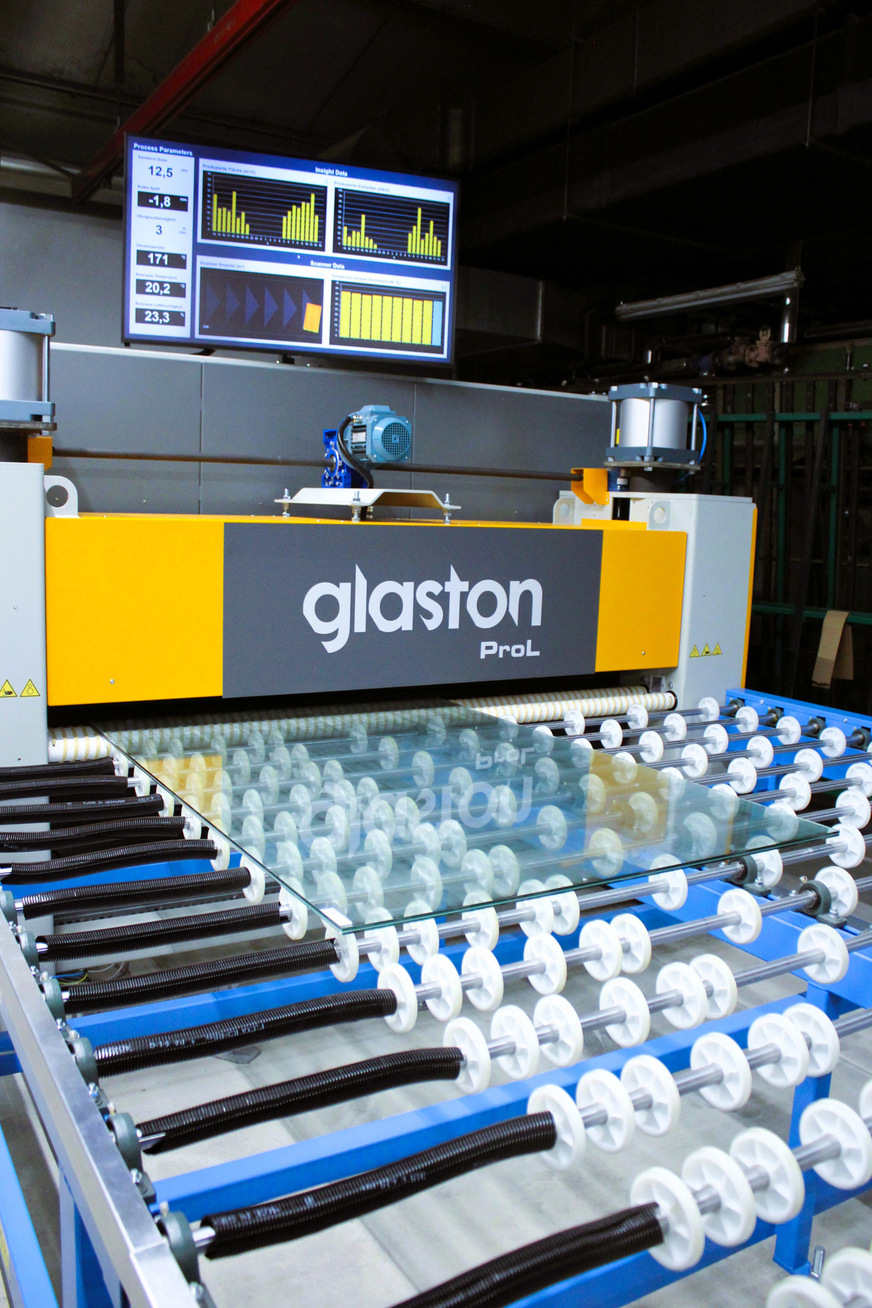
Glaston
Bei der Aufrüstung wurden die alten Heizkammern und beide Presswalzenpaare durch nur eine Heizkammer und ein Walzenpaar ersetzt sowie ein Berichtssystem und ein Thermoscanner hinzugefügt. Die Ergebnisse übertrafen alle Erwartungen, so die Beteiligten.
Im Januar 2024 war die Anlage in nur 15 Tagen wieder in Betrieb - inklusive Schulung des Bedienpersonals und sogar einer erfolgreichen Abnahmeprüfung mit Spezialprodukten.
Effizienz steigern, Energie sparen
Der „geteilte Antrieb (Split Drive)", eine bahnbrechende Funktion des Upgrades, hat sich bereits bezahlt gemacht. Zwei Antriebe ermöglichen es, dass ein neues Sandwich in die Heizkammer einfährt, wenn das vorherige die Mitte erreicht hat, selbst wenn die Sandwiches leicht unterschiedliche Dicken haben.
Das verkürzt die Wartezeit der Mitarbeitenden im Reinraum und erhöht die Kapazität erheblich. Auch eine Vorsortierung nach Sandwichdicke ist nicht mehr nötig, ein Arbeitsschritt entfällt.
Viel weniger manuelle Eingriffe
Auch die Eingriffe des Personals in die Steuerung und Eingabe der Prozessparameter wurden deutlich reduziert, wenn nicht sogar ganz eliminiert. Die Mitarbeitenden müssen nur noch bei speziellen Produkten die Parameter manuell eingeben. Die meisten Produkte werden automatisch hergestellt, wobei das System die richtigen Parameter einstellt.
Alle im Werk sind davon begeistert. „Wir drücken einfach einen Knopf und müssen uns nicht mehr um die Einstellungen kümmern. Wir erhalten eine konstante und einwandfreie Qualität am Ende der Linie", sagt Julian Lobinger, Projektleiter Technik. "Trotz der anspruchsvollen Natur unserer Produkte ist dieser Modus zu 90 % zuverlässig und garantiert uns eine gleichbleibende Kapazität und Qualität."
„Auch bei den Heizkosten konnten wir mit unserer neuen Anlage 80 % einsparen. Das ergibt derzeit einen Durchschnitt von 0,02 kWh/kg Glas - ein absoluter Spitzenwert", unterstreicht Julian Lobinger.
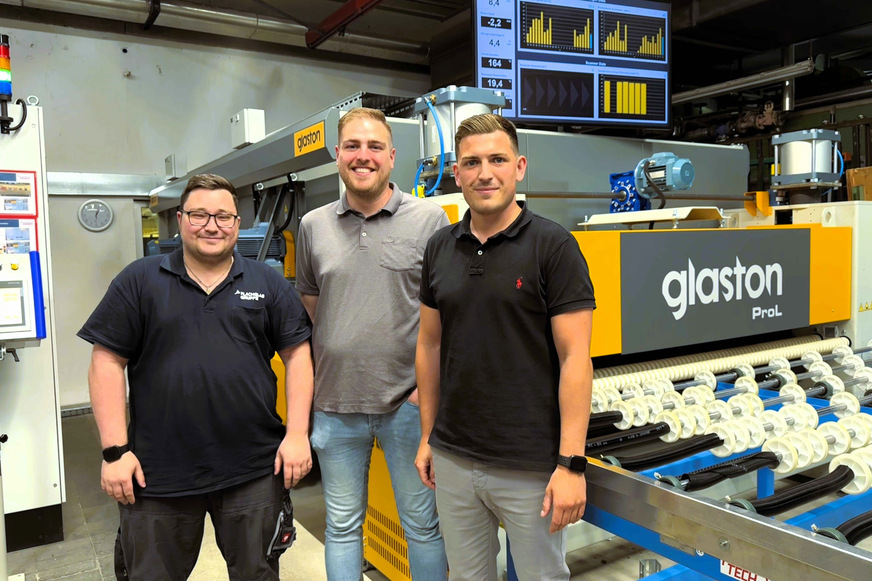
Glaston