Die Pandemie hat in einigen Wirtschaftsbereichen die Gefahr des bestehenden Fachkräftemangels nochmals verdeutlicht, auch für die Glasbranche.
Trotz bestehender technischer Ausrüstung können bei vielen Glasbetrieben aufgrund fehlender Mitarbeiter die vorhandenen Produktionslinien nicht ausgelastet werden, oder keine zusätzlichen Schichten gefahren werden. Das geht teilweise so weit, dass es schwierig wird die herkömmliche 1-Schicht Produktion am Laufen zu halten, obwohl der Markt aktuell boomt und eigentlich zusätzliche Kapazität erfordert. Viele Glasbetriebe kennen diese Probleme und suchen nach Lösungen.
Produktivitätssteigerungen bis zu 15 % ohne große Investitionen
Ein Schlüssel zur Lösung des Problems liegt in der Optimierung der Produktion und der Anpassung und Verbesserung der zugehörigen Abläufe. Solche Anpassungen machen nicht automatisch unabhängiger von Personalproblemen, aber damit lassen sich die bestehenden Ressourcen und die Produktivität im Betrieb steigern.
Je nach Komplexität der Anlagen und Arbeitsabläufe und abhängig von der Qualität der Maschinen und der Fachkräfte, können Anpassungen im Materialfluss und die Minimierung von organisatorischen Schwachstellen bereits Produktivitätssteigerungen von 5 bis 15 % bewirken.
Das Gute daran: Diese Steigerungen lassen sich kurzfristig umsetzen, verlangen in der Regel keine großen Investitionen und sind darüber hinaus nachhaltig.
Eine kamera-unterstützte Videoanalyse hilft bei der Veranschaulichung der Arbeitsabläufe und gibt dem Glas-Unternehmen bzw. seinen Verantwortlichen oftmals ganz neue Einblicke in die eigenen Produktionsabläufe sowie einen Überblick, der auch in den besten „theoretischen“ Planungen kaum darstellbar ist.
Klarerweise erreichen selbst die ausgefeiltesten Prozess-Abläufe und die angepassten Fertigungslinien irgendwann ihr technisches Kapazitätslimit. Um hier dann noch weitere Verbesserung in der Produktivität bzw. einen höheren Ausstoß zu erzielen, sind Maschinen-Adaptierungen bzw. Erweiterungen notwendig.
Automatisierung und Vernetzung als Antwort
Um mittelfristig unabhängiger von der angespannten Personalsituation zu werden, geht der Trend definitiv in Richtung Automatisierung von Prozessschritten bzw. der gesamten Produktion als Fernziel. Stichwort: Industrie 4.0!
Dabei ist die Bandbreite der Möglichkeiten enorm, beginnend bei der Automatisierung einzelner Prozessschritte, wie z. B. Etikettierung, Maschinenbestückung durch Beladeroboter bis hin zu vollständig verketteten, automatischen Produktionswerken.
Jede Automatisierung von Abläufen bringt natürlich große Vorteile mit sich, meist aber steht auf der Negativseite eine Einschränkung in der Flexibilität. Hier ist es wichtig, im Vorfeld ganz klar die Anforderungen zu definieren und aber auch Szenarien zu beschreiben, welche außerhalb des genormten Arbeitsmodus liegen und wie diese notwendige Flexibilität gewährleistet werden kann.

Foto: Denver
Automatisierung und Mitarbeitergewinnung gehen Hand in Hand?
Früher war es leicht, Mitarbeiter für den Zuschnitt zu finden, die den ganzen Tag am Brechtisch gearbeitet haben und Tonnen von Glas händisch abgestapelt haben oder im Isolierglas-Werk einige hundert Scheiben pro Tag auf die Isolierglaslinie aufgelegt und wieder abgenommen haben. Gerade für solche Arbeiten wird es heutzutage zusehends schwieriger, Menschen dauerhaft für solche Tätigkeiten zu begeistern.
Speziell im Hinblick auf die Steigerung der Attraktivität des Arbeitsplatzes in einer Glasverarbeitung, sollten deshalb primär Tätigkeiten, welche eine starke physische Belastung hervorrufen, automatisiert bzw. durch geeignete Hilfsmittel unterstützt werden.
Das macht den Arbeitsplatz nicht nur für neue, potenzielle Mitarbeiter attraktiver, sondern unterstützt auch die bewährten Mitarbeiter.
Durch den Einsatz von Hebetechnik oder von Robotern beim Anheben von Gläsern und beim Bestücken der Anlagen lassen sich auch ältere, erfahrene Mitarbeiter so unterstützen, dass sie die entsprechenden Arbeiten durchführen können.
Mit cleverem Materialfluss dem Fachkräftemangel Paroli bieten?
Die wenigsten Kunden haben den Luxus, ihre Produktionswerke optimal ausgerichtet, in beliebig großen Hallen auf der grünen Wiese zu errichten. Die Realität zeigt vielmehr, dass die meisten Unternehmen „stückweise“ wachsen und erweitern. Dies ist in Anbetracht der Investitionssummen natürlich verständlich und in den meisten Fällen auch die einzige Möglichkeit.
Eine Verlängerung der Halle hier, eine zusätzliche Produktionsfläche da, um Platz für neue Maschinen zu schaffen und die Produktionskapazität somit zu steigern ist gelebte Praxis. Diese Erweiterungen führen aber in den meisten Fällen zu starken Ineffizienzen im Materialfluss.
In vielen Fällen lässt sich durch die Umsiedelung einzelner Maschinen und dem Clustern von Produktionsschritten eine deutliche Effizienzsteigerung erzielen. Diese Zusammenführung von Produktionsschritten steigert in vielen Fällen die effektiv produktive Zeit der Mitarbeiter. Prozessbedingte Warte- oder Stillstandzeiten der Mitarbeiter können effektiver für andere Tätigkeiten genutzt werden. So konnte bei einem Kunden in Italien durch die örtliche Zusammenführung der Rahmenfertigung (Biegen und Füllen) ein Mitarbeiter eingespart und für andere Tätigkeiten eingesetzt werden. Ähnliche Möglichkeiten gibt es bei Bearbeitungsanlagen oder im Zuschnittbereich.
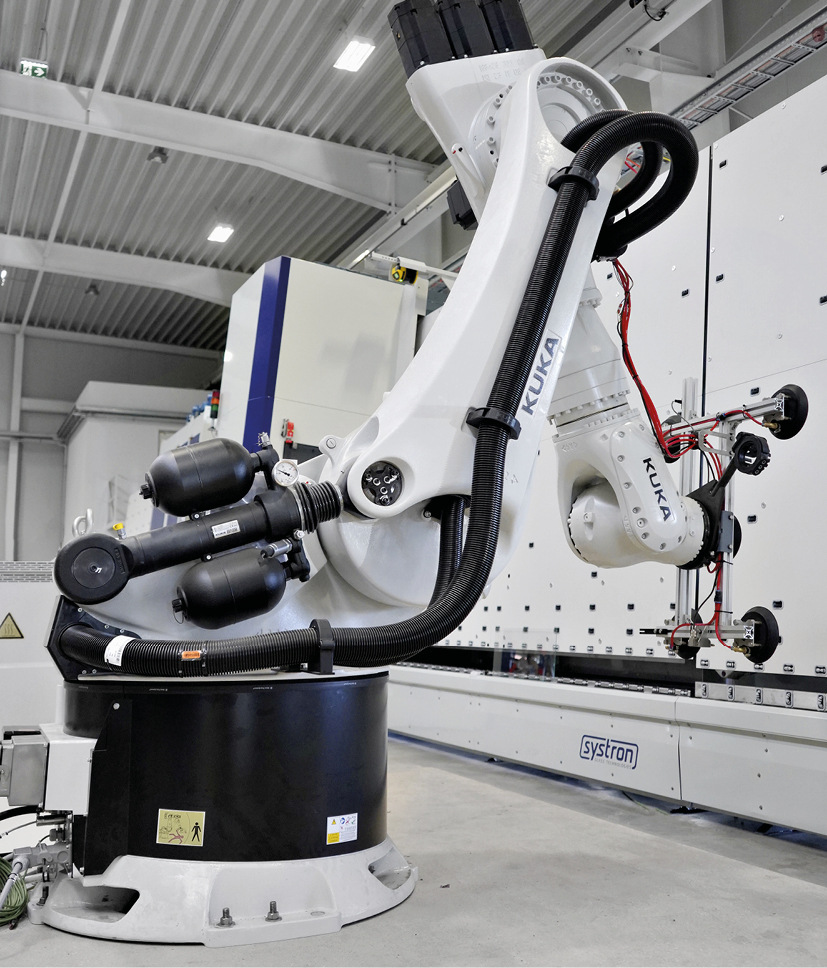
Foto: Bruckner Engineering GmbH