Bei Isolierglas steigen die Qualitätsanforderungen von Seiten der Kunden: Der Nachweis des Gasfüllgrads ist dabei ein wichtiger Punkt. Deshalb haben sich die Verantwortlichen bei Isophon für die Investition in zwei Sparklike Laser Integrated, um die Qualität der gesamten Produktion zu sichern. Die erste Anlage ist bereits in die neue ISO-Linie des Herstellers Best Makina installiert, die zweite soll in Kürze folgen.
„Die Kontrolle der Gaspresse ist entscheidend, da einige Glasaufbauten schwieriger mit Argon zu befüllen sind. Es gab in der Branche schon Fälle von unzureichender Gasfüllung und sehr teurem Ausschuss. Qualität ist sehr wichtig, um heute am Markt zu bestehen", so Torsten Bold, der Inhaber von Isophon.
Neben der Kontrolle der Gasfüllung ist der Sparklike Laser Integrated auch hilfreich bei der Einstellung und Wartung der Gasfüllanlage. Die schlüsselfertige Installation der Laser-Anlage ging schnell und einfach vonstatten.
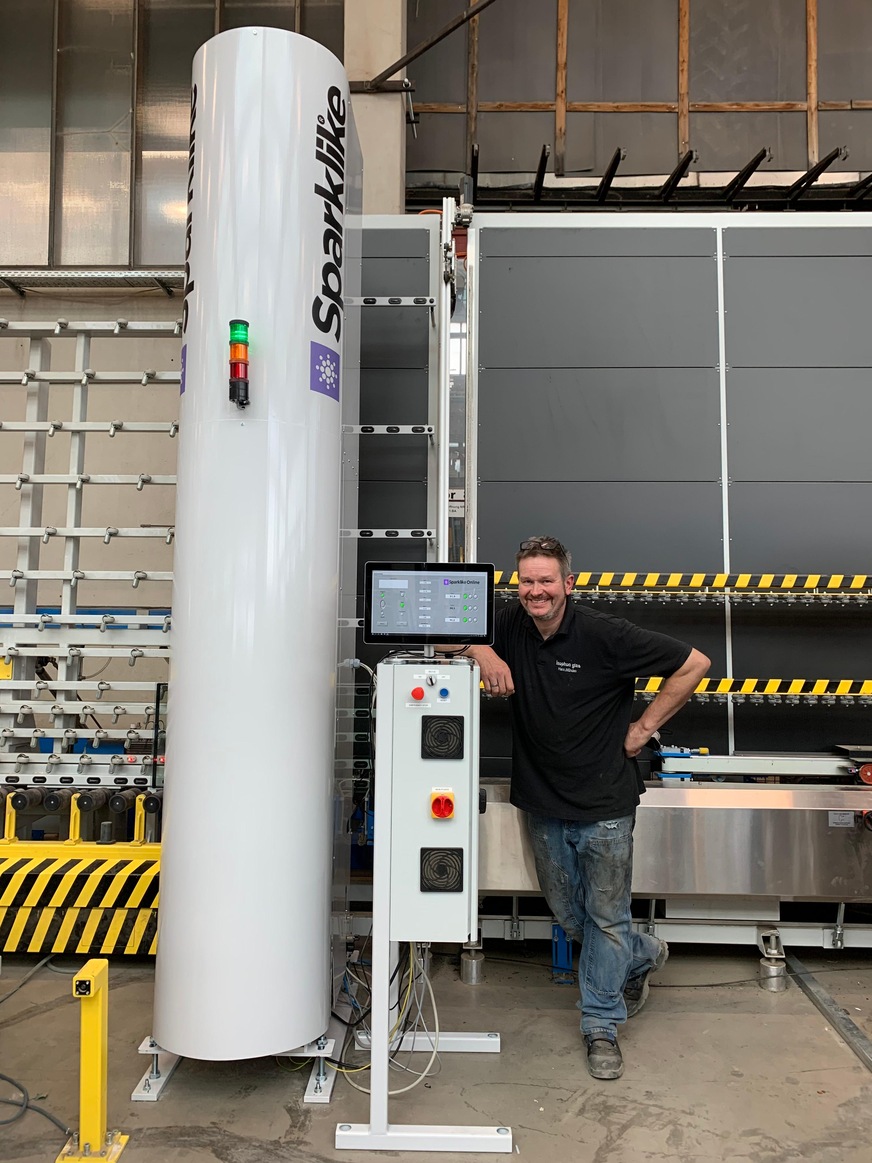
Sparklike
Der Sparklike Laser Integrated basiert auf einer Lasertechnologie, die eine zerstörungsfreie Messung der Gaskonzentration im Scheibenzwischenraum ermöglicht. Dabei lassen sich automatisiert im Fertigungsprozess 2-fach- und 3-fach-ISO-Einheiten prüfen. In Zusammenarbeit mit dem finnischen Anbieter Sparklike (www.sparklike.com/en) installierte Isophon Glas im Mai 2021 die ersten Sparklike-Messstation, eine zweite folgt im Juni.
Wie lange dauerte die Montage und Einrichtung des Sparklike Lasers bei Isophon?
Die Spezialisten von Sparklike führten den Aufbau der Prüfanlage in wenigen Stunden durch und die Integration in die Isolierglas-Linie erfolgte direkt im Anschluss. Die Prüfeinheit lief wie geplant an. Gleich die erste ISO-Einheit, die auf der neuen Linie gefertigt wurde, durchlief dann die Laser-Prüfstation, welche die ISO-Einheiten nach der Gasfüllpresse detektiert.
Die Messstation benötigt 700 mm freie Fläche in der X-Achse. Dabei ist es ist möglich, die Station so in eine ISO-Linie zu integrieren, ohne diese zu „berühren“. Die Sparklike-Anlage kann in jede bestehende sowie neue Isolierglas-Linie eingebaut werden.
„Die Montage und das Einfahren unserer Prüfstation dauerte insgesamt nur 2 Tage, einschließlich der Integration in die Isolierglas-Linie, die von Hersteller Best Makina durchgeführt wurde“, so Kai Niiranen, Entwicklungsingenieur bei Sparklike.
Die Prüfstation war bei Hersteller Sparklike im Werk in Finnland voran getestet worden, so dass sie einfach an ihren Platz in der Linie gehoben werden und am Boden verschraubt werden musste, bevor sie angeschlossen wurde.
Torsten Bold: „Die Installation ist rund gelaufen und wir sind sehr zufrieden, dass wir nun dank des Sparklike Laser Integrated eine vollständige Qualitätskontrolle unserer Isolierglas-Produktion durchführen können.“ Die Anlage bei Isophon stehe für Kunden von Sparklike als Referenzinstallation bereit.
Auch interessant: Glaston und Softsolution: Neue Partnerschaft bei der ESG-Prüfung
Die Integration der Laser-Einheit in die neue Isolierglas-Linie von Best Makina (www.bestmakina.com/en) erfolgte in Zusammenarbeit mit den Spezialisten des türkischen Anlagenherstellers. Diese waren über eine Remote-Anbindung zugeschaltet, um einen reibungslosen Einbau zu unterstützen. Bei Bedarf kann auch der Sparklike Laser Integrated über Remote-Anbindung