Neben dem Einsatz von neuen Anlagen können glasverarbeitende Unternehmen zudem auch mit Upgrades profitieren und den Energieverbrauch in der Produktion senken. Glaston hat hier unter anderem Fortschritte bei der Energieeinsparung beim Vorspannen sowie beim Laminieren und auch bei der Isolierglas-Fertigung gemacht.
So entwickelt das Unternehmen fortschrittliche Heiz- und Kühltechnologien für hohe Glasqualität, hervorragende Energieeffizienz und zuverlässige Automatisierung.
„Unsere Anlagen zum Vorspannen von Glas sind mit fortschrittlicher Heizungssteuerung ausgestattet und ermöglichen es, die Beladungseffizienz zu erhöhen und den Energieverbrauch zu senken, ohne die Qualität zu beeinträchtigen. Mit den neuesten technologischen Lösungen kann sogar die Abschreckungsenergie optimiert werden“, unterstreicht Riku Färm, Direktor Produktmanagement Glaston Heat Treatment Technologies.
Minimierung von Energieverlusten beim Glas laminieren
Die einfachste Möglichkeit, beim Glas laminieren Energie zu sparen, ist die Umstellung von einem herkömmlichen Infrarotheizungsofen auf die Vollkonvektionstechnologie. Energieverluste werden minimiert, da die gleiche Luft im Ofen umgewälzt wird.
Die richtige Energiemenge stabilisiert dabei die Ofentemperatur. Glasverarbeitende Unternehmen berichten oft von Energieeinsparungen von mindestens 50 % nach einer Umstellung der Heiztechnik auf die Vollkonvektionstechnologie.
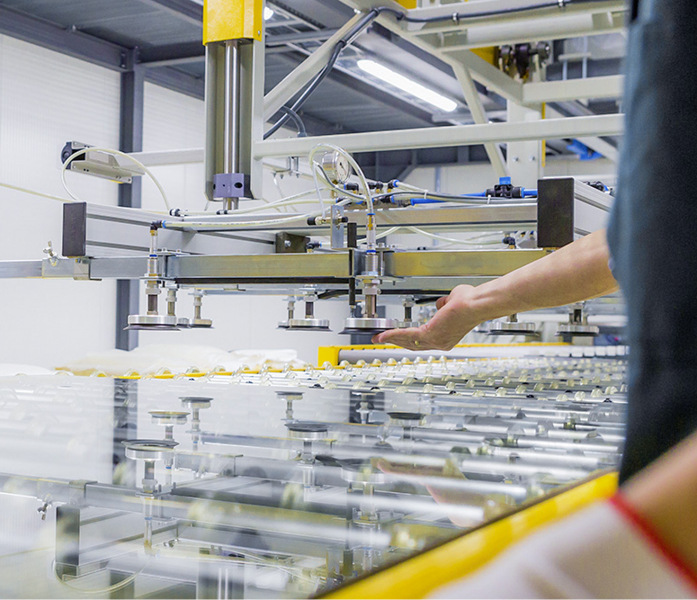
Foto: Glaston
Konvektion auch bei der Verarbeitung von Autoglas
Auch beim Biegen und Härten von Automobilglas minimiert die Konvektionsheizung den Energieverlust während des Prozesses. Sie sorgt für eine gleichmäßige Erwärmung beim Biegen von klaren und bedruckten Glasflächen. Bei der Bearbeitung von Windschutzscheiben und Schiebedächern minimiert die Konvektion die Anzahl der altmodischen Reflexionsplatten und spart so mehr Energie pro produzierter Einheit.
„Bei der Vorverarbeitung von Autoglas kann die Energie sogar zurückgewonnen werden. Durch das Abbremsen der Werkzeuge mit Elektromotoren wird Energie in das Netz zurückgespeist. Darüber hinaus sparen unsere leichtgewichtigen Komponenten bis zu einem Drittel der Energie ein, die herkömmliche Maschinen benötigen“, sagt Robert Prange, SVP Glaston Automotive & Display Technologies.
Energie sparen bei der Isolierglas-Produktion
Mit der Glaston TPS-Technologie benötigen Unternehmen nur eine einzige Maschine anstelle mehrerer Komponenten zur Herstellung der Isolierglas-Einheiten. Das TPS-System synchronisiert mehrere Prozesse zu einem einzigen, so dass die tägliche Produktion aufgrund von kürzeren Taktzeiten früher abgeschlossen werden kann und dadurch Energie eingespart wird.
„Beim Glas-Reinigungsprozess schaltet die Trockenzone unserer Glasplatten-Waschmaschine automatisch ab, wenn die Glasplatte trocken ist. Dadurch wird der Energieverbrauch der Waschmaschine um 25 % gesenkt, während der geschlossene Wasserkreislauf den Wasserverbrauch weiter reduziert“, sagt Uwe Risle, Direktor Produktmanagement Glaston Insulating Glass Technologies.
Mehr Energie durch Upgrades
Ein sicherer Weg, die Energieeffizienz zu gewährleisten, ist die Wartung der Anlagen zusammen mit den Glaston-Experten und Original-Ersatzteilen.
Die Aufrüstung einer bestehenden Glasverarbeitungsanlage mit der neuesten Technologie führt zu erheblichen Energieeinsparungen, ohne dass in eine völlig neue Anlage investiert werden muss.
„Die meisten unserer neuesten Technologien sind als Upgrade erhältlich, so dass die Kapazität schnell und effizient erhöht, die Qualität und Ertrag verbessert, der Wartungsaufwand reduziert und die Betriebszeit verbessert werden kann“, kommentiert Artturi Mäki, SVP Glaston Services.
Mehr über Energieeffizienz in der Glasverarbeitung finden Sie unter https://glastory.net
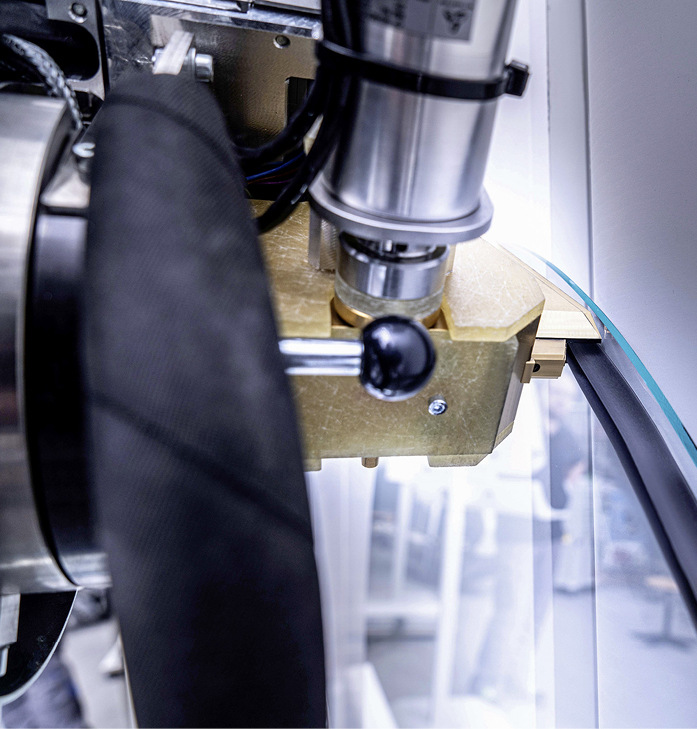
Foto: Glaston