1921 gegründet, plant und fertigt die Stocker Fensterbau GmbH am Standort Uttenweiler mittlerweile in 3. Generation Holzfenster, Holz-Aluminium-Fenster und Aluminiumfenster. Das Team um Geschäftsführer Jens Stocker scheint vieles richtig gemacht zu haben in der Vergangenheit, schließlich hat das Unternehmen gerade in den letzten Jahren deutlich zulegen können. Um dem stetigen Wachstum gerecht zu werden, die Produktionsprozesse in der Holzfensterbeschichtung zukunftsgerecht aufzustellen und die Kapazität zu erhöhen, entschieden sich die Verantwortlichen 2021 zur Investition in eine komplett neue vollautomatisierte Lackieranlage mit modernster Fördertechnik, Flutanlage, leistungsfähigem Lackierroboter und Halogentrockner – und vertraute jahrzehntelange Expertise von Range + Heine. Jens Stocker: „Die Planung und das Anlagenkonzept haben uns von Anfang an überzeugt.“
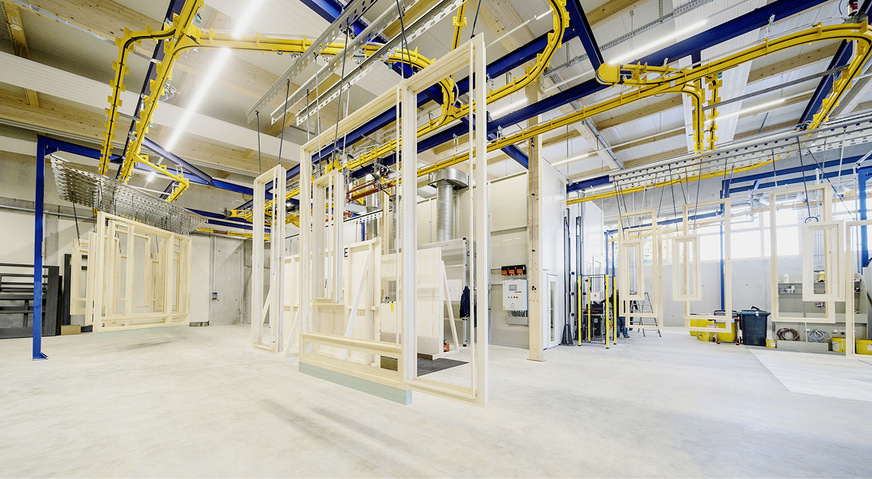
Foto: Range + Heine
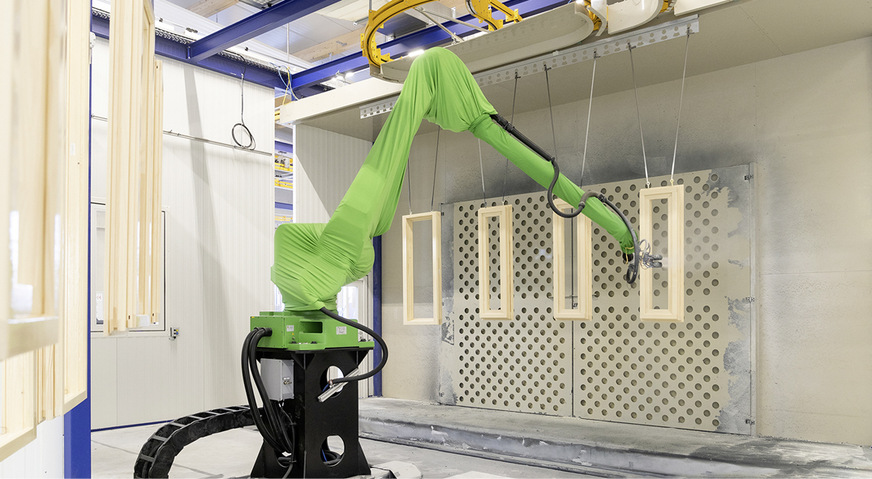
Foto: Range + Heine
Effiziente Prozesse + Top-Qualität
Der Beschichtungsprozess vollzieht sich mit der neuen Anlagentechnik wie folgt: Zunächst werden die Holzelemente an Traversen gehängt. Über die Fördertechnik gelangen die Bauteile dann zu den einzelnen Stationen der Anlage. Im ersten Schritt erfolgt die Imprägnierung und Grundierung der Fensterelemente in der Flutanlage vom Typ flowcomat P+ mit der Imprägnierung Aquawood Primo von Adler. Die Flutanlage ermöglicht bei Bedarf auch einen schnellen manuellen Farbwechsel und ist daher besonders flexibel einsetzbar. Nach Durchfahren der Flutanlage gelangen die Holzrahmen in einen speziellen Abtropfbereich. Dabei werden die an den Traversen hängenden Elemente für ca. 15 min schräg gestellt, um das Abtropfverhalten zu optimieren. Zusätzlich unterstützt eine Befeuchtung (Luftfeuchte 65 %) das Abtropfen des Flutlacks. Im Anschluss erfolgt die Flutlacktrocknung durch ein Halogensystem. Dieses ermöglicht in einem Zeitrahmen von ca. 50 min die schonende Trocknung der Holzbauteile rein über Lichtstrahlen.
Range + Heine Geschäftsführerin Claudia Max-Heine: „Durch die Trocknung der Elemente von innen nach außen stellen sich die Holzfasern weniger stark auf. So gestaltet sich die auf den Beschichtungsprozess folgende Nachbearbeitung in der Schleifanlage weniger aufwendig.“
Vollautomatische Beschichtung per Robotertechnik
Im nächsten Schritt übernimmt der mit neuester Computertechnik und 2D plus-Erkennung ausgestattete CMA-Lackierroboter die Applikation der Zwischenbeschichtung Aquawood Intermedio ISO von Adler für farblose Aufbauten bzw. von Aquawood Intercare für deckende Beschichtungen. Dabei wird das Element beim Einfahren gescannt bzw. fotografiert und dann über eine Dicken- und Schräglagenerkennung genauestens eingemessen – daraufhin wird vollautomatisch das entsprechende Lackierprogramm ausgelöst. Max-Heine: „Durch die 2D plus-Erkennung ist gewährleistet, dass der Roboter immer parallel zur Werkstückoberfläche lackiert.
Damit werden Schichtstärkenunterschiede infolge schräger Aufhängungen fast komplett vermieden.“ Zudem ist durch den optimierten Lackierbewegungsablauf auch ein manuelles Nachjustieren kaum noch notwendig. Und falls doch, lässt sich dies ganz mit der zum Roboter gehörenden Panel-Steuerung erledigen.
Danach erhalten die mit der Zwischenbeschichtung versehenen Elemente im hängenden Zustand einen manuellen Zwischenschliff. Über spezielle Senkstationen lässt sich die optimale Bedienhöhe für den Lackierer einstellen.
Im letzten Schritt spritzt der Lackierroboter den Decklack auf: Für deckende Beschichtungen verarbeitet das Unternehmen den Decklack Aquawood Covatop von Adler, transparente Beschichtungen für Holz-Alu-Fenster werden mit Aquawood Natureffekt gefertigt.
35 Fenstereinheiten lassen sich so in einer Schicht bewältigen. Dabei sind alle Fenster-Arten und Bauteil-Geometrien bis zu 4,50 m Länge und 3 m Höhe zu verarbeiten – vollautomatisch und nahezu ohne manuelle Nacharbeiten.
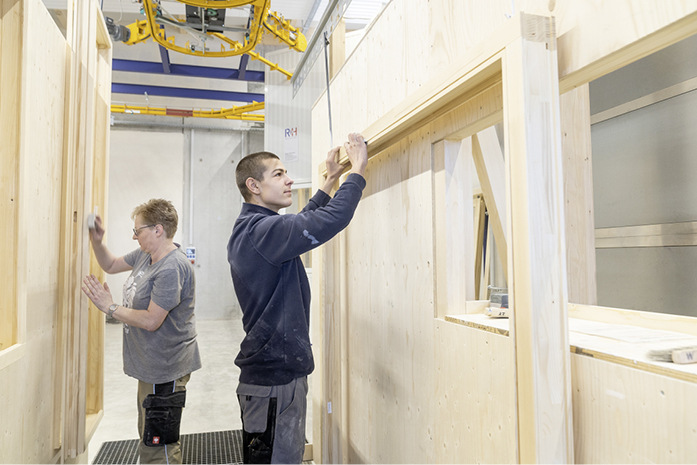
Foto: Range + Heine
Nachhaltiges Anlagenkonzept
Bei der Anlagenplanung stand auch das Thema Nachhaltigkeit immer wieder im Fokus. Dank neuester Technologien trägt die von Range + Heine realisierte Beschichtungsanlage zur Schonung der Umwelt bei. Zum Beispiel werden alle im Flutkreislauf anfallenden Abwässer in einer Spülwasserkoagulier-Anlage (R+H waco 200) gesammelt und mithilfe von Chemikalien entflockt bzw. wieder aufbereitet. Das saubere Wasser wird abgeleitet und das Restmaterial kann im Hausmüll entsorgt werden. Ein weiteres Detail: Durch spezielle Vorabscheider vor die Absaugung in der geschlossenen Spritzkabine müssen die Verbrauchsfilter weniger häufig gewechselt werden und auch der Reinigungsaufwand ist geringer. Zudem bleibt die Absaugleistung dauerhaft kontant – was eine saubere Kabinenluft garantiert.
Bei der Auswahl des Beschichtungsmaterials ist Nachhaltigkeit ein wichtiges Thema: Die Wasserlacke des österreichischen Herstellers Adler bürgen dabei für verlässliche Qualität und für gute Umwelteigenschaften – die stumpfmatte Fensterlasur Aquawood Natureffekt ist sogar mit dem Kreislaufwirtschafts-Zertifikat Cradle to Cradle ausgezeichnet.
Die neue Fertigungsanlage ist nun seit Ende 2021 im Einsatz. Geschäftsführer und Unternehmensinhaber Jens Stocker zeigt sich hochzufrieden: „Die vollautomatische Anlage sorgt bei unseren Mitarbeitern für eine deutliche Arbeitserleichterung und steigert unsere Qualität. Auch das Zusammenspiel mit den Fensterbeschichtungen von Adler funktioniert sehr gut – das Team hat die Beschichtungen optimal auf die Anlage angepasst. Der Roboter beschichtet sehr gleichmäßig und auch die Oberflächenstruktur unserer Holzfenster ist so deutlich besser geworden. Eine Investition, die sich auf jeden Fall rechnet.“
www.range-heine.de
www.adler-lacke.com
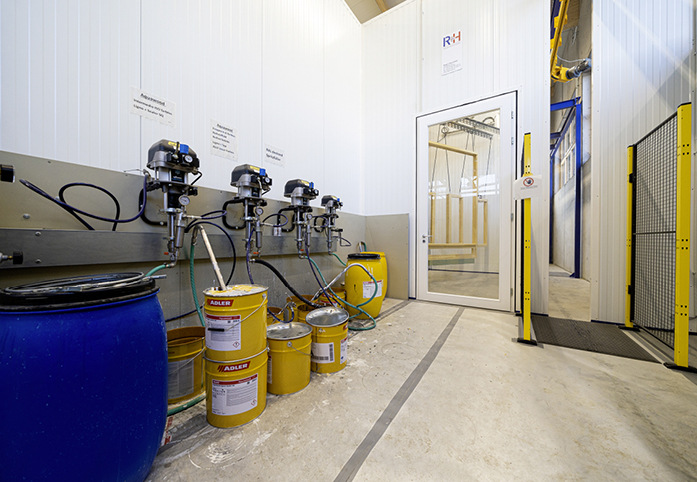
Foto: Range + Heine