Mein letzter Besuch bei Fensterbau Müller in Essen liegt noch nicht so lange zurück – bereits vor zwei Jahren war ich echt beeindruckt über diese „Fensterfertigung par excellence“, wie ich sie damals betitelt hatte. Wie sich das Familienunternehmen aber jetzt nochmals weiterentwickelt hat, hin zu einem durchdigitalisieren und verketteten Fertigungsbetrieb, ist wirklich faszinierend. Was sich aber nicht geändert hat, sind die Platzverhältnisse: Das Unternehmen mit rund 100 Mitarbeitern verfügt über eine sehr begrenzte Produktionsfläche von 6500 m² ohne Erweiterungsmöglichkeiten – eingezwängt zwischen Stadtpark, Straße und Bahngleisen. Es gilt also, die Platzressourcen geschickt ausnutzen. Mehr noch: Die Holzfensterexperten haben die Not zur Tugend gemacht und nutzen jeden Quadratmeter des Firmenareals aus, weil hier modernste Bearbeitungsaggregate intelligent verkettet sind. In den letzten drei Jahren wurden so rund 25 Mio. Euro in die Anlagentechnik investiert – mittlerweile kann man wohl von der modernsten und schnellsten Holzfensterproduktion Deutschlands sprechen.

Foto: Daniel Mund / GLASWELT
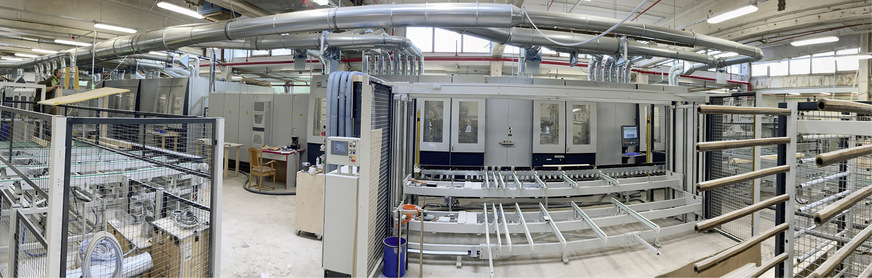
Foto: Daniel Mund / GLASWELT
Dieser Anspruch wird bereits beim Wareneingang deutlich: Das vom Zulieferer (Holz Schiller) für die Projekte kommissionierte Holz wird von einem Roboter der Maschinenfabrik Springer direkt auf die Mechanisierung der Kapphobellinie vor der Conturex-Systemanlage aufgelegt. Dabei ist der Roboter (3 m Aktionsradius) in der Lage, die Weinig-Anlage mit vier Teilen pro Minute zu bedienen. Diese dürfen bis zu 100 kg schwer oder gar 4,5 m lang sein – der Holzlieferant achtet dabei genau auf die geforderte Teilepositionierung, wenn etwas fehlt, geht der Roboter selbstständig auf Suchfahrt.
Eindrucksvoll auch die Holzspanverwertung: Eine neue Absaugung (Höcker Polytechnik) sorgt dafür, dass jegliche Holzreste thermisch verwertet werden können. Da das Unternehmen bereits nach zwei Monaten die Späne für den Eigenbedarf gebunkert hat, entwickelte man die große Lösung für „den Rest“ der Jahresproduktion: Dabei kam es Familie Müller darauf an, verkaufsfähige Verpackungseinheiten zu generieren. Matthias Müller: „Jetzt können wir baumarktgerechte Holzbriketts anbieten, die bei uns automatisch verpackt werden. Die Energiepreise schießen bekanntlich in die Höhe – unsere Briketts erzielen immer höhere Erlöse, mittlerweile erhalten wir für eine Palette (1 Tonne) bis zu 300 Euro.
Durchlaufzeit halbiert auf einen Tag
Müller verdeutlicht den High-Speed-Takt, der hier vorherrscht: „Wir geben morgens um 7 Uhr das kommissionierte Holz zum Abstapeln, um 8 Uhr wird der Rahmen auf die Traverse für die Oberflächenbehandlung gehängt, mittags können wir Flügel und Blendrahmen fertig lackiert davon abhängen und um 16 Uhr stehen die Bauelemente fertig verpackt zur Auslieferung bereit.“
Bemerkenswert sind die nicht üppig ausgelegten Pufferanlagen – schon allein aus Platzgründen: 200 Isolierglasscheiben können eingelagert werden, was eine Tagesproduktion darstellt. Dazu gibt es noch ein Außenlager, in dem zwei bis drei Tageslieferungen gelagert werden. Die Zulieferer müssen also wirklich just in time mitspielen, bei den Mengen, die hier verarbeitet werden. „Denen ist die Bedeutung der pünktlichen Lieferung aber auch bewusst,“ so Müller. Eine besondere Rolle fällt in Bezug auf die Materialversorgung der Firma Nüssing zu: Oliver Hombrink als Nüßing-Produktmanager erläutert die umfassende Beratungskompetenz seines Hauses: „Wir befassen uns mit dem Baubeschlagshandel und auch mit der Oberflächentechnik. Dabei übernehmen wir nicht nur die Logistik, sondern auch die technische Betreuung. Dadurch ergänzen wir durch unsere Anwendungstechniker die Beratungsaufwände unseres Beschichtungs-Partners Adler. Hier bei Müller hatten wir die glückliche Situation, dass wir wussten, was geplant ist, und konnten die Adler-Produkte so einstellen, dass sie für die Objektgrößen und den Anspruch bei der Fa. Müller optimal passen.“
Müller selbst zeigt sich offensichtlich begeistert von der Qualität seines Beschichtungslieferanten: „Gerade was den lasierenden Bereich angeht glauben wir, mit Adler einen Top-Beschichtungslieferanten gefunden zu haben.“ Dietmar Tölle als Nüßing-Gebietsleiter ergänzt: „Wir können auf die verschiedenen Beschichtungsmengen in unseren Lagern in Dortmund und Verl immer zurückgreifen. Auch die Beschlagsversorgung haben wir natürlich im Griff, dafür bin ich zweimal in der Woche hier beim Kunden.“
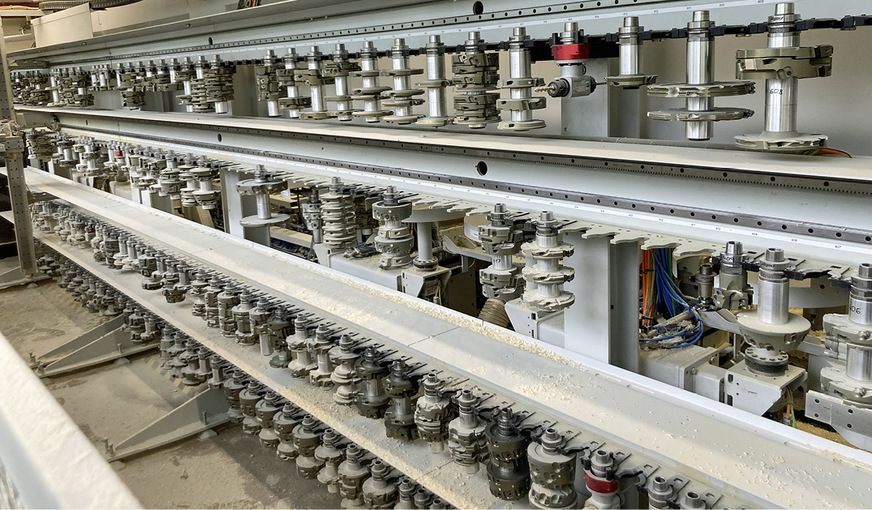
Foto: Daniel Mund / GLASWELT
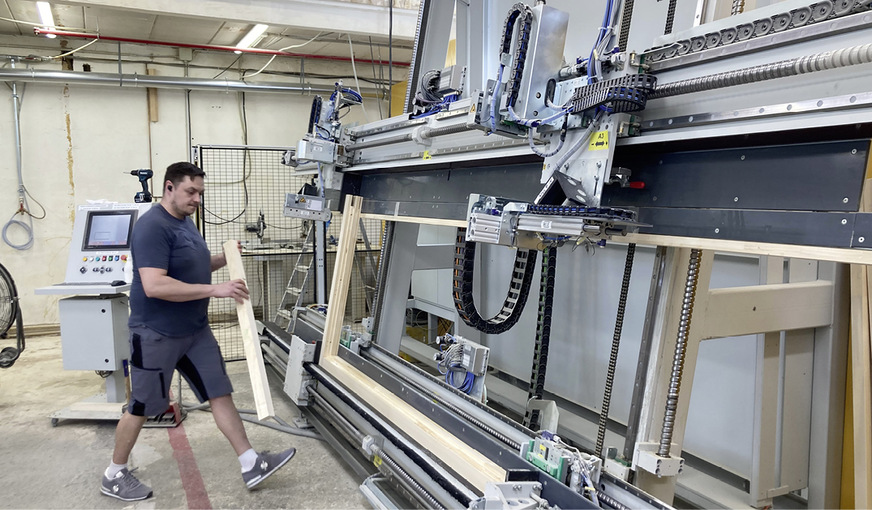
Foto: Daniel Mund / GLASWELT
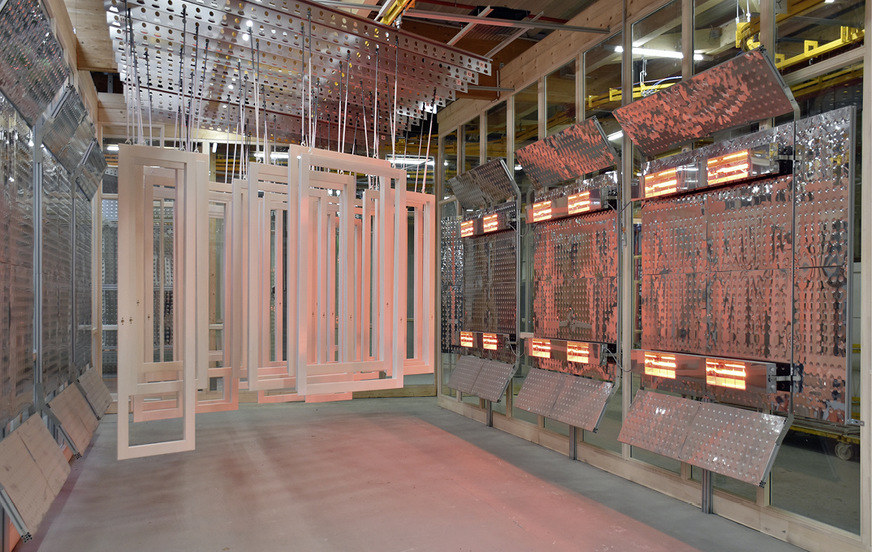
Foto: Daniel Mund / GLASWELT
Wer steuert die Abläufe?
Die Steuerung dieser riesigen Werkstoffmengen und der Produktionsanlagen stellt eine enorme Herausforderung dar, da kommt es auf die richtige Software und die intelligente Bedienung an. Müller vertraut hier auf ProLogic FenOffice. Die Konstruktions- und Produktionssoftware hat dabei alles unter Kontrolle, von der Projektverwaltung über die Maschinenschnittstellen und Produktion bis hin zur Logistik und entsprechenden Auswertungen.
Natürlich kommt es auf die detailgenaue Kommunikation der Anlagen mit der Fensterbausoftware an: Die Anlagen von Lemuth (z. B. Flügel- und Rahmenmontage), Weinig, Springer und S&S Maschinenbau (elektrische Rahmen- und Flügelpresse) sowie die komplette Oberflächen-Infrastruktur von Range + Heine sind umfassend an die Fensterbausoftware angeschlossen, alle Informationen aus der Produktion, aus den Projektdaten und aus der Logistik ergeben ein großes Ganzes. Der verantwortliche Prologic-Projektmanager Jan Megier während des Rundgangs: „Das geht so weit, dass wir beispielsweise auch die Rezeptur des Lacklieferanten Adler steuern, schließlich muss die richtige Farbe am richtigen Flügel ankommen.“
Sonderbau abgeschafft
Beim Rundgang durch die Fensterproduktion wird deutlich, wie beharrlich die Fensterfamilie Müller an den Abläufen feilt: Beispielsweise bei der automatischen Beschlagsmontage mit der Lemuth-Anlage. Hier werden neben den Standard-Bändern auch die Schwerlastbänder von Roto („Power Hinge“) automatisch gesetzt.
Trotz der Enge war es den Fensterexperten ein wichtiges Anliegen, Fenstergrößen mit 4,5 × 3,4 m realisieren zu können. Dabei hat sich der mengenmäßige Durchsatz in den letzten beiden Jahren deutlich ausgeweitet: Sprach man vor zwei Jahren noch von einer Umsatzgrößenordnung über 30 Mio. Euro, so berichtet Matthias Müller von einem herausfordernden letzten Jahr mit Umsätzen jenseits der 40-Mio.-Schwelle – trotz umfangreicher Umbaumaßnahmen.
Erstaunlicherweise wird dieser hohe Umsatz einschichtig bewältigt. Müller erklärt: „Die Organisation des Personals und des Materialflusses rund um den Betrieb ist schon im Einschichtbetrieb eine echte Herausforderung, deswegen bleiben wir dabei.“
Umbau am offenen Herzen
Die Installation der Lackieranlage von Range + Heine stellte eine besondere Herausforderung dar – schließlich ging die Produktion ungebremst weiter. Jetzt verfügen die Holzfenster-Experten über eine Flutanlage für die Grundierung und eine Zwischen- und Endbeschichtung, die jeweils über zwei Roboter erledigt wird. Die Ansteuerung läuft über Barcode und einen Leitrechner. Michael Max, technischer Leiter bei Range + Heine blickt zurück: „Allein schon in der Layoutphase hatten wir einige Klippen zu überspringen, bis das Anlagenlayout den Anforderungen genügt hat – die äußert knapp bemessenen räumlichen Gegebenheiten und die Forderungen nach maximaler Kapazität galt es in Einklang zu bringen.“
Auch die Montage der CNC-Anlage von Weinig gehörte nicht zu dem, was man sonst als „das haben wir immer schon so gemacht“ bezeichnet – schon allein aufgrund der Tatsache, dass neben den beengten Platzverhältnissen auch noch Hallenpfosten innerhalb der Anlage zu integrieren waren. Weinig-Vertriebsmanager Stefan Röder berichtet, dass man die Anlage und die Platzverhältnisse im Weinig-Werk exakt simuliert habe.
„Nur so konnten wir sicherstellen, dass beim Montagetermin auch wirklich alles gepasst hat.“ Und Produktmanager David Eberhardt ergänzt: „Es gibt bislang nur zwei vergleichbare Anlagen von Weinig. Hier allerdings haben wir jetzt die schnellste CNC-Anlage überhaupt realisiert.“
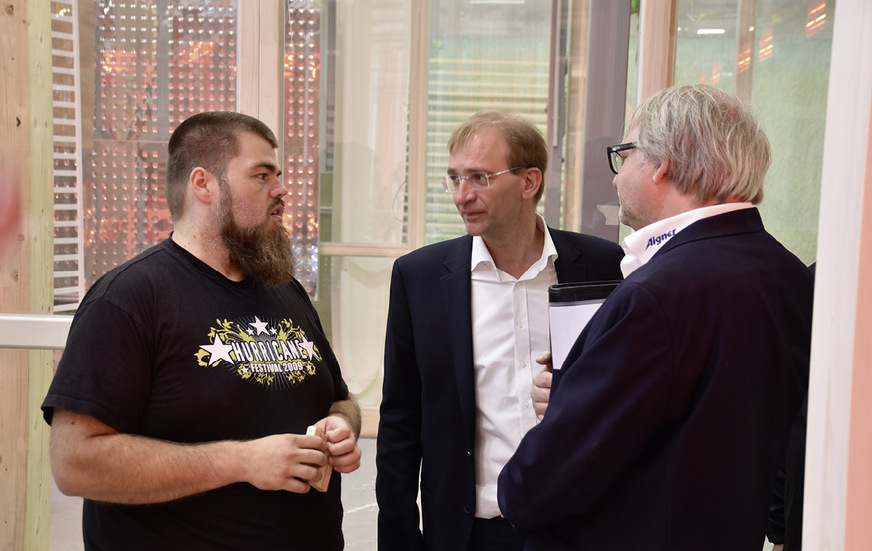
Foto: Daniel Mund / GLASWELT
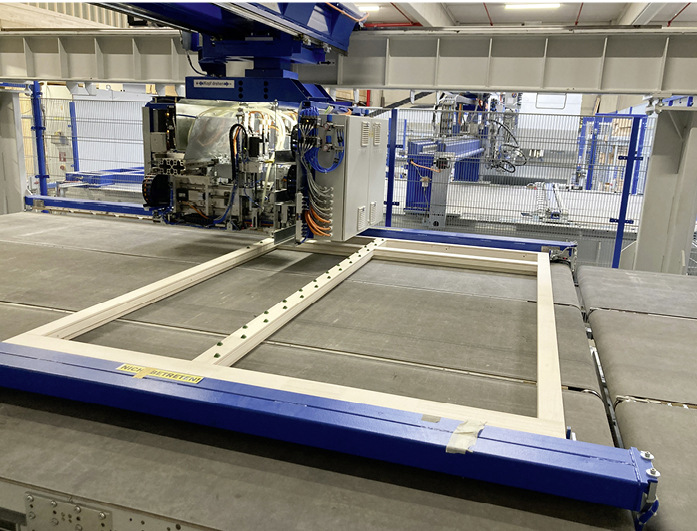
Foto: Daniel Mund / GLASWELT
Holz-Aluminium im Fokus
Zusammen mit dem Werkzeuglieferanten Aigner aus Österreich kommen jetzt Werkzeuge für 32 Fenstersysteme (für Holzstärken von 68, 78, 92, 110, 120 mm in Holz und Holz-Alu) zum Einsatz. Der Schwerpunkt bei Müller liegt dabei deutlich auf der Premium-Werkstoffkombination Holz und Aluminium: „Aktuell liegt der Holz-Alu-Anteil bei über 95 Prozent“, gibt Stephan Müller zu Protokoll.
Für Aigner bedeutete die Werkzeugausstattung das bisher umfangreichste Einzelprojekt, berichtet der geschäftsführende Gesellschafter Josef Hochholzer. Die Werkzeuge für den Längsbereich wurden mit der Aigner High-Speed-Technologie ausgestattet, welche eine Schnittgeschwindigkeit von bis zu 120 m/s zulässt.
Hochholzer: „Damit lässt sich die Performance der Maschine voll auszunutzen.“ Ein weiterer Grund für den hohen Durchsatz ist die Verwendung der Schlitz- und Zapfen-Verbindung. Allerdings bringt das auch große Werkzeug-Durchmesser mit sich. Dennoch finden aber alle Werkzeuge im riesigen Werkzeuglader (660 Plätze) Platz, sodass jederzeit alle Systeme ohne Belegungswechsel produziert werden können.
„Einfach zu handeln“
„Uns ist immer viel daran gelegen, dass das Ganze am Ende auch einfach zu benutzen bzw. zu handeln ist,“ bringt es Matthias Müller am Ende des Rundgangs auf den Punkt. „Wir benötigen eine klar strukturierte Erfassungsebene, womit auch unterschiedliche Bediener zurechtkommen.“ Diese habe man mit der Software von Prologic gefunden. Prologic-Mann Megier: „Die Maschinensteuerung selbst ist vielleicht gar nicht die größte Herausforderung. Das können wir und vielleicht andere auch. Was uns auszeichnet, ist die Kommunikationsebene: Herr Müller nimmt Kontakt zu uns auf, wenn er eine neue Idee hat und wir setzen es dann auch direkt um.“
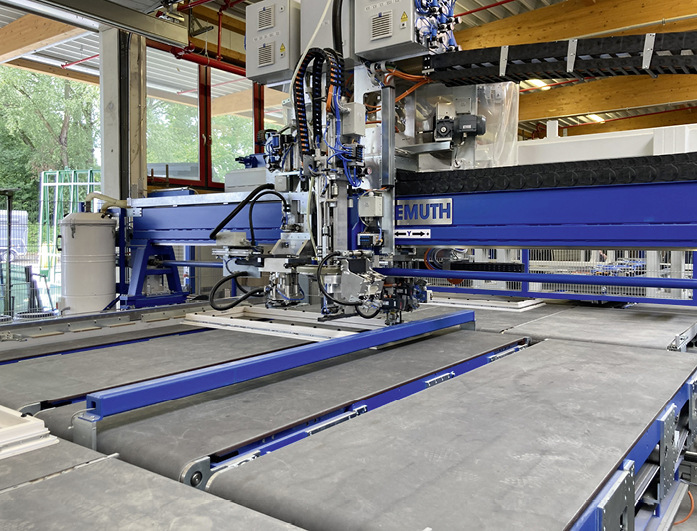
Foto: Daniel Mund / GLASWELT
Steckbrief Müller Holzfensterbau
Holz- und Holz-Aluminium-Fenster (Sicherheitsfenster bis RC 3, Denkmalschutzfenster)
Umsatz 2021 über 40 Mio. Euro, geplant für 2022 über 50 Mio. Euro
Kapazität über 80 000 Fenstereinheiten/Jahr
Mitarbeiter: Insgesamt 100, davon in der Produktion ca. 40
Aluschale: Batimet, Gutmann
Beschlag: Roto
Holzlieferant: Schiller
Software: Prologic
Conturex Systemanlage und Aigner Werkzeugbestückung
www.weinig.com
www.aigner-werkzeuge.at
Weitere Kontaktadressen der Lieferanten
Beschlags- und Glasmontage mit Lemuth-Anlage
Die Glas- und Beschlags-Montagelinie von Lemuth erledigt folgende Arbeiten vollautomatisch:
Alle Umstellungen auf unterschiedliche Fenstertypen, Fenstergrößen und Profiltypen erfolgen vollautomatisch ohne Taktzeitverlust. Das Übergeben der lackierten Fensterelemente in die Linie erfolgt ebenfalls automatisch.