Glaswelt – Sie haben den easy-LAM IFL mit Fokus auf Automatisierung entwickelt, geben Sie bitte Details dazu, und spart das Manpower ein?
Robert A. Gaiser – Ja. Die Automatisierung bei der Glaslaminierung ermöglichen wir durch mehrere Faktoren: Es fallen der Vorverbund und der Autoklav weg, das verkürzt die Vorbereitungszeiten deutlich. So entfällt das manuelle Handling der Gläser sowie die Vorbereitung von Hordewagen. Auch nach der Laminierung werden die Hordewägen obsolet. Insgesamt rechnen wir durch die Reduzierung der manuellen Prozesse mit einem Einsparungspotential von bis zu 80 Prozent, abhängig von Arbeitsweise des VSG-Herstellers.
Glaswelt – Wie fertigt man Sonder- und Modellgläser oder freie, dreieckige, runde Formen?
Daniel Klaus – Mit der easy-LAM IFL lassen sich alle Arten von Gläsern laminieren, sie müssen nur die vorgegebenen Mindestdimensionen erfüllen. Ob quadratisch, rund oder dreieckig, mit oder ohne Aussparung, spielt keine Rolle. Eine Mindestdimension geben wir auch nur deshalb vor, da wir beim Einfördern die Abstände der PINs im PIN-System der Vakuumpresse berücksichtigen müssen. Unterschreiten wir die Mindestgröße so kann es zu einem frühzeitigeren Kontakt mit der Heizplatte kommen. Für Projekte mit kleineren Gläser können wir den Abstand der PINs nach Kundenwunsch anpassen.
Glaswelt – Wie effizient lässt sich die Charge belegen?
Gaiser – Aktuell arbeiten wir mit einer Nutzfläche von 2600 × 5000 mm und einer Fläche von 13 m2. Wir empfehlen die Chargen möglichst effizient vorzubereiten, um so eine hohe Flächennutzung zu erzielen, sprich von 60 - 80 %, was jedoch auch immer abhängig von den Produkten des Kunden ist. Mit vielen gleichen Gläsern, lässt sich eine sehr hohe Nutzung erreichen. Werden viele unterschiedliche Größen gefahren oder hat jedes Glas eine andere Größe, empfiehlt es sich vor der VSG-Linie eine Vorsortierung mit Softwareoptimierung einzusetzen.
Glaswelt – Wie energieeffizient ist die easy-LAM IFL?
Klaus – Bei der Energieeffizient stellen wir gerne den Vergleich zu den aktuellen Energieverbräuchen ohne unseren easy-LAM IFL her, das liefert beeindruckende Ergebnisse. Aus den Werten der Realproduktionen unserer Kunden sowie Messungen durch Interessenten, bestätigen wir regelmäßig die von uns versprochene Senkung von 50 % gegenüber einem Vorverbund + Autoklav-Prozess. Die Verarbeiter sparen in zwei Kalenderjahren die Energieverbräuche eines Autoklavs für eine gesamte Jahresproduktion.
Glaswelt – Wie kann die Anlage in bestehende Fertigung integriert werden?
Gaiser – Da der Vorverbund, die Hordewagen-Preparation und der Autoklaven entfallen. können wir unsere Anlage direkt nach dem Legebereich im Reinraum positionieren. Dies hat den Vorteil, dass die Gläser horizontal transportiert werden. Im Legeberich wird dann die Charge für den easy-LAM IFL gebildet. Die Entnahme nach der Lamination läuft aktuell meist noch manuell, zudem besteht auch hier die Möglichkeit, die Gläser zu den nächsten Prozessschritten weiter zu fördern oder per Roboter zu entnehmen. Wir bieten hier verschiedene Möglichkeiten an, die wir individuell auf den Kunden abstimmen.
Glaswelt – Welche Weiterentwicklungen strebt Bürkle beim easy-LAM IFL künftig an?
Klaus – Aktuell steht die Optimierung der Produktionsabläufe mit dem easy-LAM IFL im Fokus. Wir wollen eine automatische Qualitätskontrolle integrieren und die Bedienerfreundlichkeit weiter erhöhen. Weiter arbeiten wir kontinuierlich an kürzeren Prozesszeiten, um die Kapazität der Anlage auszubauen. Und beim Produkthandlings arbeiten wir an Konzepten, um die Chancen besser vorzubereiten und den Automatisierungsgrad weiter zu erhöhen. Im Zusammenhang mit der Digitalisierung starteten wir vergangenes Jahr mit ersten Datenanalysen zum Aufbau von Software-Services im Sinne von Industrie 4.0 und IIOT.
Glaswelt – Spannend ist Ihr Forschungsprojekt für 3D-PV-Module mit dem Fraunhofer-Institut. Wollen Sie 3D-Sicherheitsgläser laminieren, Ähnlichkeiten beim Laminieren bestehen schließlich durchaus?
Klaus – Das Forschungsprojekt für 3D-PV-Module ist in 2021 gestartet. Wir entwickeln in Zusammenarbeit mit dem Fraunhofer Institut einen neuen Laminator für gebogene PV-Module. Vor allem im Fahrzeugbau könnten diese Module eingesetzt werden. Ziel ist, die Reichweite von Elektroautos zu erhöhen. Sicherlich bestehen bei der Laminierung von Sicherheitsgläsern und PV-Modulen Ähnlichkeiten, allerdings befinden wir uns erst am Anfang der Entwicklung des neuen Laminators. —
Die Fragen stellte Matthias Rehberger
Halle 12, Stand A21
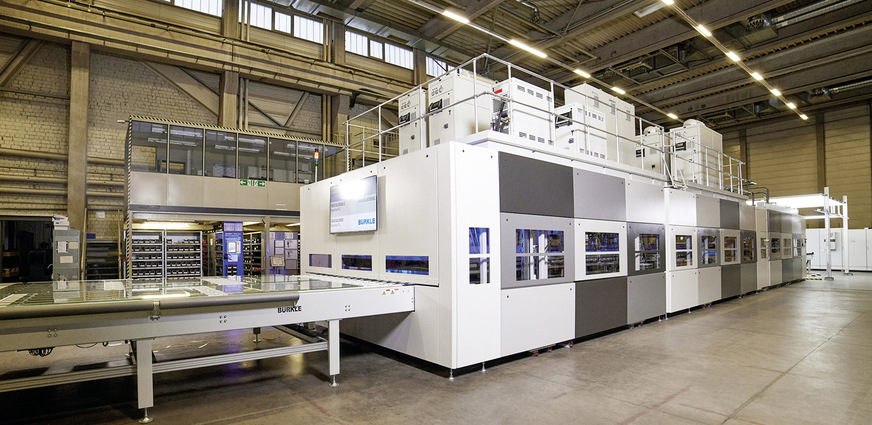
Foto: Bürkle
Webinar ansehen
Das GLASWELT-Webinar zur Bürkle Technologie finden Sie unter