Spiegel helfen uns, Bewegungen im Tanzstudio zu kontrollieren, Licht in fensterlose Räume zu bringen, unser Aussehen in der Umkleidekabine zu prüfen oder neue Perspektiven zu eröffnen. Sowohl in privaten als auch in gewerblichen und öffentlichen Bereichen sind sie feste Bestandteile der Ausstattung. Dabei können sie eine Reihe unterschiedlicher Funktionen erfüllen. Mal sind sie Arbeitsinstrument, mal stehen ästhetische Aspekte im Vordergrund oder sie erfüllen zusätzliche Aufgaben.
Wo ist laut Regelwerken eine erhöhte Sicherheit relevant?
Vor allem in Bereichen, die öffentlich zugänglich sind, regelmäßig von vielen Menschen aufgesucht werden oder in denen sich spielerisch oder sportlich bewegt wird, spielt die Sicherheit auch beim Einsatz von Spiegeln eine große Rolle.
Grundlegend gilt als Regelwerk für „Glas im Bauwesen“ die DIN 18008 mit ihren Teilen 1-6. Hier wird mit der neuen Fassung 2020 der erhöhte Einsatz von sogenanntem „Glas mit sicherem Bruchverhalten“ gefordert.
Zusätzlich gelten für den öffentlichen Bereich weitere Anforderungen aus u. a. Unfallvorschriften des DGUV oder Arbeitsstättenverordnungen, um das Unfallrisiko für dort beschäftigte Personen zu minimieren.
Genauer bedeutet das: Besondere Maßnahmen zur Verhütung von Verletzungen bei Glasbruch sind überall dort erforderlich, wo Personen und hier vor allem Kinder und Sporttreibende während des Bewegungs- und Verkehrsablaufs auf verglaste Wände, Wandteile oder Türen treffen können. Ursachen hierfür können sein: stolpern, gestoßen werden, Unachtsamkeit, unzureichende Beleuchtung oder Panik.
Spiegel in ihrer meist genutzten Funktion an Wänden oder auf/in Möbeln fallen aber i.d.R. nicht unter die DIN 18008, da sie als „Möbel“ nicht als „Glas im Bauwesen“ gesehen werden. Gerade im privaten Bereich gibt es somit keine wirklichen Anforderungen mehr – im Gegensatz zum öffentlichen Bereich und/oder zu Sportstätten, wo es zusätzliche Regelwerke gibt, die an die Sicherheit, auch mit Spiegeln, appellieren!
Auch wenn Spiegel in den meisten Einbausituationen nicht unter die Anforderungen der DIN 18008 fallen, gibt es doch andere anerkannte Regeln der Technik, wie z.B, die „Technische Richtlinie Nr. 11 – Spiegel – Handhabung und Montage (5. Auflage 2014)“ des „Bundesinnungsverbands des Glaserhandwerks, BIV“.
Diese Richtlinie bietet Planern, Handwerkern, Glasern etc. Sicherheit beim Einsatz von Spiegeln mit bewährten und praktikablen Methoden. Sie zeigt, welche Arten von Spiegeln, unter anderem auch mit bruchsicheren Eigenschaften, es gibt und wie diese zu handhaben sind. Zusätzlich zu diesen Anforderungen bestehen aber, wie oben schon genannt, in manchen Bereichen weitere Anforderungen, wie beispielsweise in Sportstätten. Dort müssen Verglasungen zusätzlich ballwurfsicher nach DIN 18032-3 sein. I.d.R. wird eine solche Ballwurfsicherheit durch Verglasungen mit „bruchsicheren Eigenschaften“ hergestellt.
Was heißt, dass man durch den Einsatz von VSG oder ESG auf der sicheren Seite ist. Sind Spiegel mit Sicherheitseigenschaften gefordert, müssen diese entweder aus ESG nach DIN EN 12150-1 oder VSG nach DIN EN 14449-1 bestehen.
Doch lassen sich nicht alle Spiegel zu ESG oder VSG verarbeiten, was entweder andere Methoden oder Verarbeitungsschritte mit sich zieht. Gerade industriell ist es derzeit „nur“ möglich, Spiegel entweder mit entspanntem Floatglas nach DIN EN 572-2 oder zum Teil auch als VSG oder Verbundglas (VG) herzustellen. Da die i.d.R. verwendete Silberschicht eine thermische Vorspannung zu ESG nicht unbeschadet übersteht, kann hier nur eine nachträgliche Verspiegelung stattfinden. Aber gerade dann können Verwerfungen, wie sie bei ESG entstehen, deutlicher sichtbar werden.
Garantiespiegel: Eine andere Möglichkeit wäre das thermische Vorspannen von „Garantiespiegeln“, welche keine Silberbeschichtung nach DIN EN 1036-1 aufweisen, sondern z. B. mit einer Chromschicht nach DIN EN 1096-1 versehen werden – wie der Chromspiegel Mirastar.
Eine Besonderheit ist die „Spionspiegel“-Wirkung von Mirastar, mit der sich auch raffinierte Gestaltungslösungen realisieren lassen: Liegt die Spiegelschicht auf der Seite des helleren Raums, entsteht dort ein Spiegeleffekt; vom dunkleren Raum aus kann man dagegen in den helleren hineinsehen.
Oft kommen bei monolithisch verwendeten Spiegeln auch sogenannte „Splitterschutzfolien“ zum Einsatz, welche, je nach Anforderung, auf der Vorder- oder Rückseite angebracht werden können.
Die letzte Möglichkeit ist, entweder zwei Spiegel oder einen Spiegel und eine Floatglasscheibe mittels einer PVB-Zwischenschicht zu einem Verbund herzustellen. Aber hier ist zu unterscheiden, ob diese Zwischenschicht mittels Glas/Glas-Kontakt oder mit der Lackschicht zur Zwischenlage hergestellt wird. In Deutschland gilt nur der Verbund zum Glas als VSG. Befindet sich der Spiegellack zum Verbund, handelt es sich lediglich um ein Verbundglas (VG).
Glasrückenspiegel: Eine Variante für höchste Belastungen ist der Glasrückenspiegel. Dieser besteht aus einem Glas mit Spiegelbeschichtung, auf dessen Rückseite zum Schutz der Silber- und Lackschicht eine zusätzliche Floatscheibe aufgebracht wird.
Glasrückenschutzspiegel wurden speziell entwickelt für Einsatzbereiche wie Nassräume mit außergewöhnlich hoher, permanenter Luftfeuchtigkeit oder aggressiven Dämpfen; sowie auch für ein Umfeld, das den Einsatz chemischer Reiniger erfordert, wie Schwimmbäder, Heilbäder, Saunen, Schulen und Kindergärten, Krankenhäuser oder Pflegeheime, wo ein erhöhter Schutz gegen Beschädigung der Silber- und Lackschichten gefordert ist.
Bei solchen Spiegeln handelt es sich nicht um Spiegel mit Sicherheitseigenschaften gemäß den gelten Regelwerken, auch wenn eine gewisse Splitterbindung vorhanden ist.
Sicherer Spiegel für die Umwelt
Mit Miralite Pure hat Saint-Gobain einen Spiegel entwickelt, dessen blei- und lösemittelfreie Zusammensetzung dem gestiegenen Umwelt- und Gesundheitsbewusstsein entspricht. Ein optimiertes, ressourcenschonendes Verfahren erlaubt den Einsatz von nur einer Schicht Schutzlack, das den Lackverbrauch um 20 % senkt.
Der Spiegel besteht zudem zu 30 % aus recyceltem Glas. 30 % des bei der Produktion verbrauchten Wassers wird aufbereitet und wiederverwendet und 100 % der Metalle, seltenen Erden und des Bruchglases werden recycelt.
Der Lack auf Wasserbasis enthält keinerlei aromatische Lösungsmittel (Xylol), 70 % weniger Lösungsmittel und entspricht der Decopaint-Richtlinie 1 (zulässiger Grenzwert für den Gehalt: 130 g/l). Auf diese Weise wird die Arbeitssicherheit in den Produktionsanlagen verbessert. Frei von Bleizusatz, kann es einfach recycelt werden.
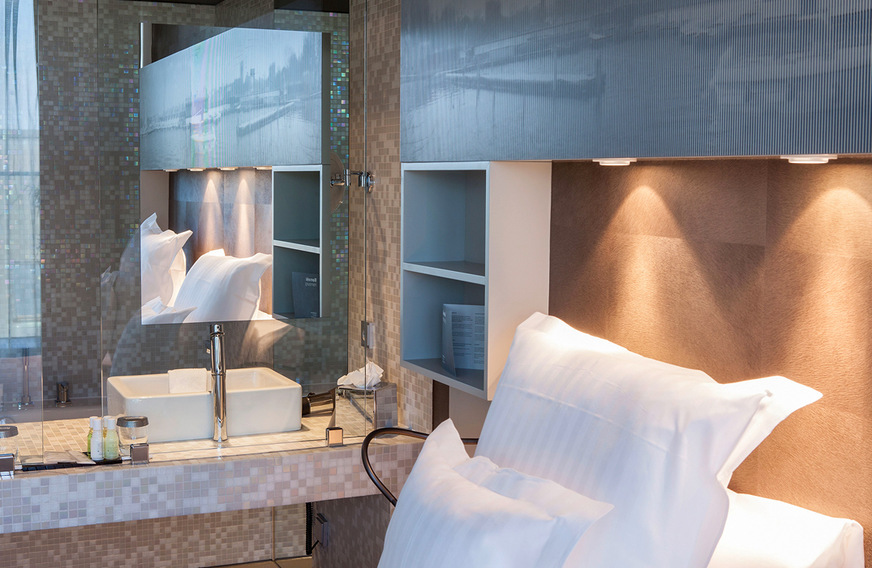
Foto: Saint-Gobain Deutsche Glas / Christoph Seelbach