„Für unsere Kundenberatung ist das ein sehr elementarer Schritt“, erklärt Inhaber und Geschäftsführer Dietmar Heil, „denn in unserer laufenden Produktion in Hüntwangen war dieses aufgrund der guten Auslastung schon seit einiger Zeit nicht mehr optimal durchführbar“. Herzstück des Innovationscenter ist die Darstellung von Produktion 4.0 im textilen Bereich, bei der Lager & Handlingsysteme, Zuschnitt, industrielles Nähen und Ultraschall-Schweißen oder Kleben im Mittelpunkt stehen.
„Haben wir früher dem Kunden gezeigt wir seine zukünftige Maschine funktioniert, so hat der Kunde heute nach einer entsprechenden Einweisung die Möglichkeit, in unserer Ausstellung Markisentücher zu produzieren“, erzählt Heil und ergänzt: „ er kann sogar seine eigenen Leute mitbringen und so alle wichtigen Mitarbeiter live in die Entscheidungsprozesse bei der Umstellung der Produktion einbinden“. Offene Fragen sollen so direkt vor Ort und ausgesprochen zielführend beantwortet werden können, um die Entscheidungprozesse zu vereinfachen bzw. zu beschleunigen.
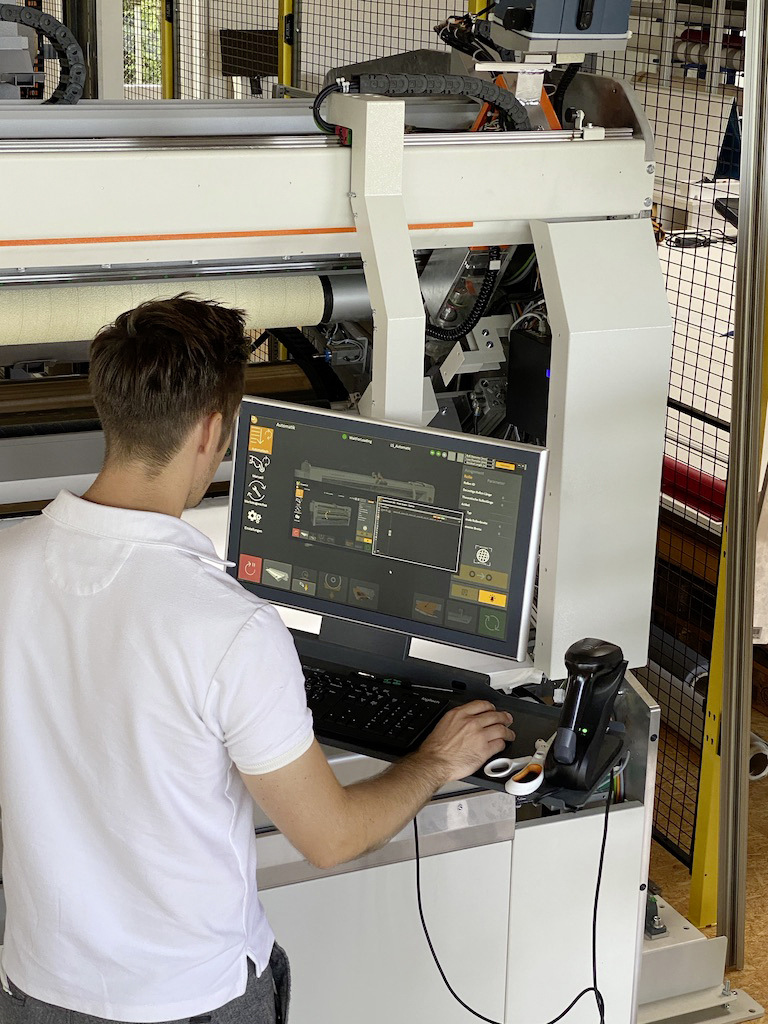
Foto: Olaf Vögele
Das Herzstück der Anlage
Das RegalLagerSystem RLS ist ein dynamisches Stoffballenlager mit automatischer einer direkten Stoffballenbereitstellung an die ScreenCut oder auch indirekt über eine Auslagerstation zu anderen Maschinen. Das System arbeitet dynamisch und unabhängig zu der Zuschnittmaschine. Direkt an ScreenCut gekoppelt arbeitet das System überlappend. Ein-/Auslagerprozesse der Stoffballen vom Lager werden auch dann vollzogen, wenn der Zuschnitt arbeitet und keine Rolle anfordert. Das installierte RLS ist so optimiert, dass z.B. 1 × 3,6 m oder 3 × 1,2 m breite Ware auf einer Lagerebene (chaotisches Lagersystem) Platz finden. Ein automatisierter Ballenwechsler sorgt für die Abkopplung zur ScreenCut und entlastet das Personal bezüglich des Ballenhandlings. Das optionale Verknüpfen mit der Kundenauftragssoftware läßt nahezu keine Stillstandzeiten und Fehlerquellen zu.
Das Handling beim Zuschnitt zählt
Wird mit einem Auftragspool gearbeitet wird, können die benötigten Stoffballen durch die „Look ahead“ Funktion automatisch bereitgestellt und bei Auftragsstart dynamisch in der Abzugsposition verbracht werden. Das heißt, dass während eines Zuschnitts auf der ScreenCut schon der Ballen für den nächsten Auftrag bereitgestellt wird und ein anschließendes Umwechseln innerhalb von wenigen Sekunden möglich ist. Ebenso werden alle für den Zuschnitt relevanten Daten eingelesen und auch das Design auf dem Bildschirm dargestellt. Zeitgleich zum Verarbeitungsstart bzw. direkt nach dem Stoffballenwechsel, wird der vorher verarbeitete Stoffballen eingelagert und die Stoffdatenbank aktualisiert. Anschließend erfolgt ein weiteres Bereitstellen des Stoffballens für den nächsten Auftrag.
Die zu schneidende Materialrolle auf der ScreenCut wird je nach Ausstattung der Maschine manuell oder mittels technischer Hilfseinrichtungen in die Rollenmulde an der Frontseite der Maschine eingelegt. Nach Dateneingabe und Erfassung der Materialbreite, errechnet die Maschine die Position der Längsschneider wobei die Positionierung automatisch erfolgt. Die Dateneingabe erfolgt manuell mittels DDE über Touchscreen oder mittels Barcode und Computer. Ein Software-Modul ermöglicht den Datenaustausch vom Netzwerk des Kunden zur Maschine und zurück. Im nächsten Arbeitsschritt wird das Material millimetergenau auf die programmierte Länge transportiert, gleichzeitig in Längsrichtung geschnitten und aufgewickelt.
Sobald die zugeschnittene Bahn fertig aufgewickelt ist, leuchtet das Fach an der Einlagerstation des MHS auf, in welches der aktuelle Auftrag gelegt werden soll. Beim Schließen des Aufwicklers wird die nächste Zuschnitt Sequenz automatisch gestartet. Werden zwei/drei Teilbahnen gleichzeitig geschnitten, so werden die Fächer mittels unterschiedlichen Farben angezeigt. Ebenso wird der entsprechende Teilbereich im Aufwickler beleuchtet, um Fehler zu vermeiden. Danach wird der befüllte Wagen des MHS an die Näh-/Klebestation übergeben. Dort wird die eindeutige Wagen ID erkannt und die gelagerten Aufträge auf dem TouchPanel in Listenform angezeigt.