Bereits seit über 40 Jahren produziert man so in der Mitte Deutschlands ganz nach den individuellen Wünschen und Vorstellungen der Kunden. Geschäftsführer Marcel Discher richtet sein besonderes Augenmerk dabei auf das Design, die Funktionalität und die Langlebigkeit der Produkte.
Die Überarbeitung der Werksproduktionskontrolle mit einem externen Berater war neben anderen Bereichen der Auslöser auch über die Konfektion der Markisentücher nachzudenken. Wir haben uns dann auf dem Markt umgeschaut und mit dem Schweizer Unternehmen Jentschmann einen guten Partner zum kompletten Umbau unserer Konfektion gefunden.
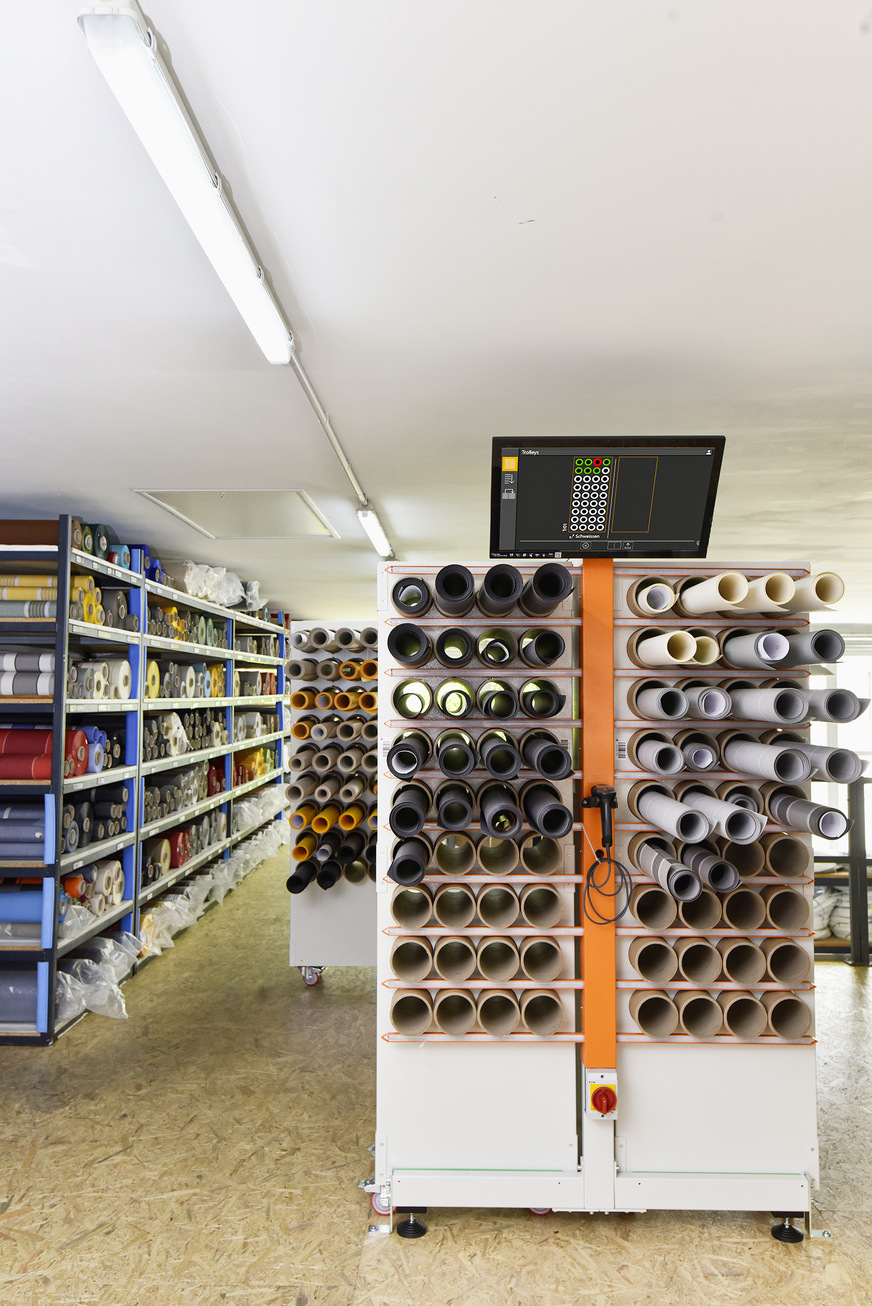
Foto: Mobau Markisen
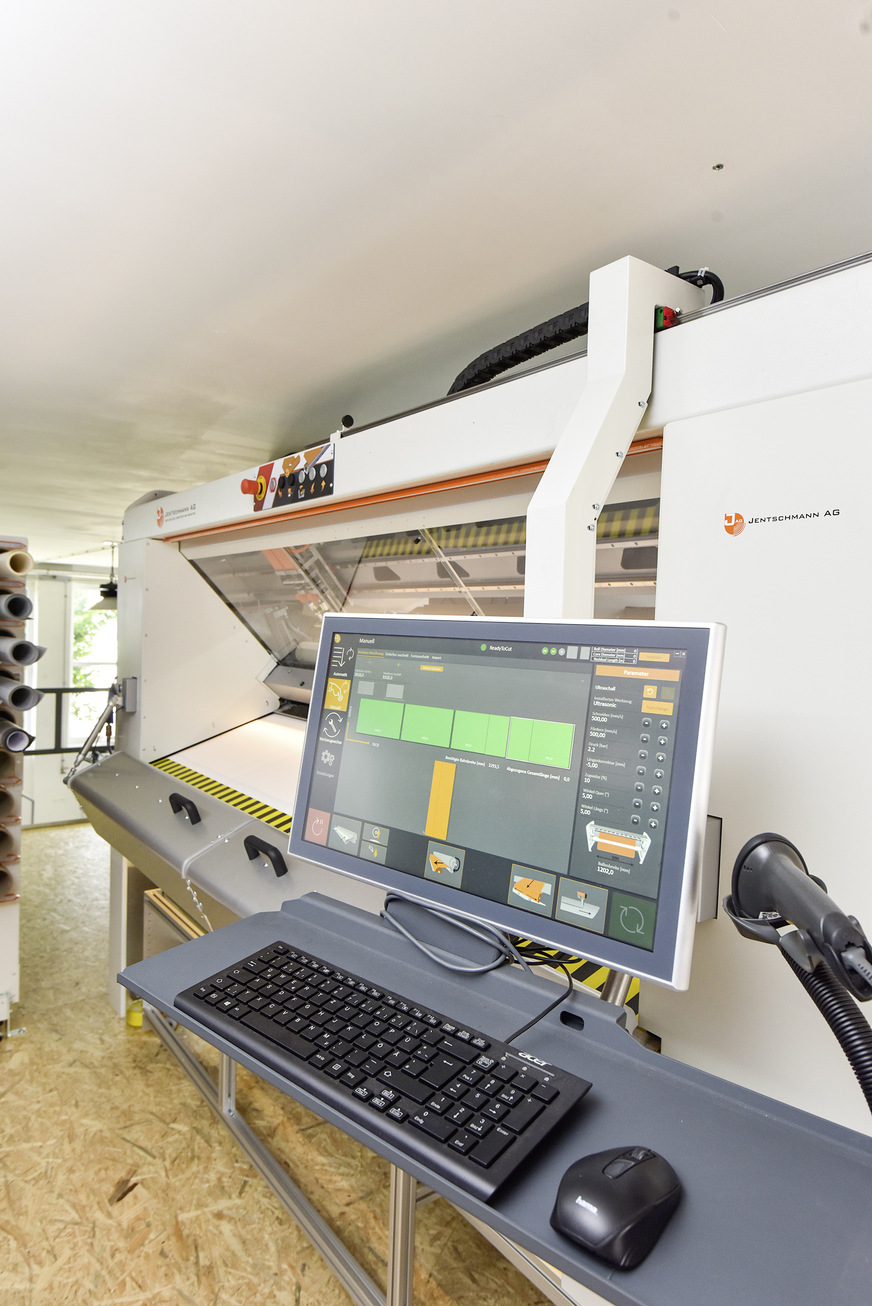
Foto: Mobau Markisen
Computergesteuerter Zuschnitt
Die ScreenCut vereint hoch entwickelte Technologien in einem unglaublich kompakten Design und bietet damit gerade bei engen Platzverhältnissen optimale Lösungen. Möglich wird das erst durch den Einsatz einer aktiv angetriebenen Umlenkwalze, die gleichzeitig als Amboss für die Ultraschall-Schneideinheiten fungiert. Der Platzbedarf der Maschine konnte dadurch um bis zu 85 % gegenüber dem Vorgängermodel reduziert werden. Die hohe Produktivität ergibt sich durch die integrierte Aufwickelvorrichtung und den Schnitt während des Materialtransportes. Erreicht wird das durch die präzise, automatische Positionierung der Ultraschall-Längsschneider und kürzeste Handlingzeiten in der Kombination mit dem Material-Handling-System MHS
Kurze, schnelle Wege
Das MHS ist ein intelligentes Transportsystem von zugeschnittenen Tüchern mit einer visuellen Unterstützung für den Bediener. Die Materialbewegungen von zugeschnittenen Tüchern zu nachgelagerten Maschinen werden so erleichtert und können auf kleinstem Raum erfolgen. Durch die Positionierungsanzeige per Bildschirm kann eine papierlose Tuchkonfektion realisiert werden. Jedes MHS besteht immer mindestens aus einer Einlagerstation (am Zuschnitt), und einem Transportwagen Auslagerstation an der Nähstation (Sewsy und Kesa).
Die Auslagerstationen sind je nach Anzahl der nachgelagerten Maschinen beliebig erweiterbar.
Das MHS hat mit eine eigene Datenbank, in der alle Aufträge nach dem Zuschnitt von der ScreenCut übergeben werden. Beim Einlagervorgang der Zuschnitte wird der Bediener von einem farblichen Leitsystem unterstützt, so dass eine Zuordnung der Zuschnitt in kürzester Zeit erfolgt. Die zugeschnittenen Aufträge werden dem Wagen zugehörig gespeichert und in der Datenbank vermerkt. Wird der Wagen dann an eine beliebige Auslagerstation angedockt, wird die eindeutige Wagen-ID erkannt und die dazugehörigen Aufträge von der Datenbank geladen. Der Bediener erhält eine Liste der eingelagerten Aufträge und kann diese anwählen. Sobald ein Auftrag ausgewählt ist, leuchtet das Lagerfach, in dem der gewünschte Zuschnitt lagert. Der Bediener verarbeitet das Tuch und quittiert, um das nächste Tuch zu erhalten.
Für Marcel Discher waren die Vorteile dieses Systems das klare Entscheidungskriterium, Jentschmann bei der Planung und Realisierung der neuen Konfektion mit an Bord zu holen. So konnten konnten die Platzverhältnisse in der Konfektion, die sich auf einer zweiten Ebene befindet deutlich optimiert, und die Arbeitsbedingungen für die Mitarbeiter angenehmer gestaltet werden.
Durchgängig hohe Qualität
Nicht nur der Zuschnitt wurde in diesem Zuge optimiert. Auch die Weiterverarbeitung der Tücher wurde neu gestaltet. Drei halbautomatische Nähanlagen Typ Sewsy wurden dazu zum rationellen und genauen Verbinden und Säumen der Markisentücher nachgeschaltet. Die Maschinen verfügen über einen synchronisiert fahrenden Zweinadel-Steppstichnähkopf mit 3-fach Transport und einer optionalen Aufwickelvorrichtung für die genähten Stoffbahnen. Die Steuereinheit mit digital überwachten Antrieben hat einen geringen Platzbedarf und wurde an das MHS angebunden. Damit wird die Konfektion auch den hohen Qualitätsansprüchen von Marcel Discher gerecht, der mit seinen Planungen schon einen weiteren großen Schritt vollzogen hat. Den Weg zur papierlosen Produktion. „Nur wenn wir ständig an uns arbeiten und nach Verbesserungen streben, können wir den Ansprüchen im Markt gerecht werden“, so Discher.
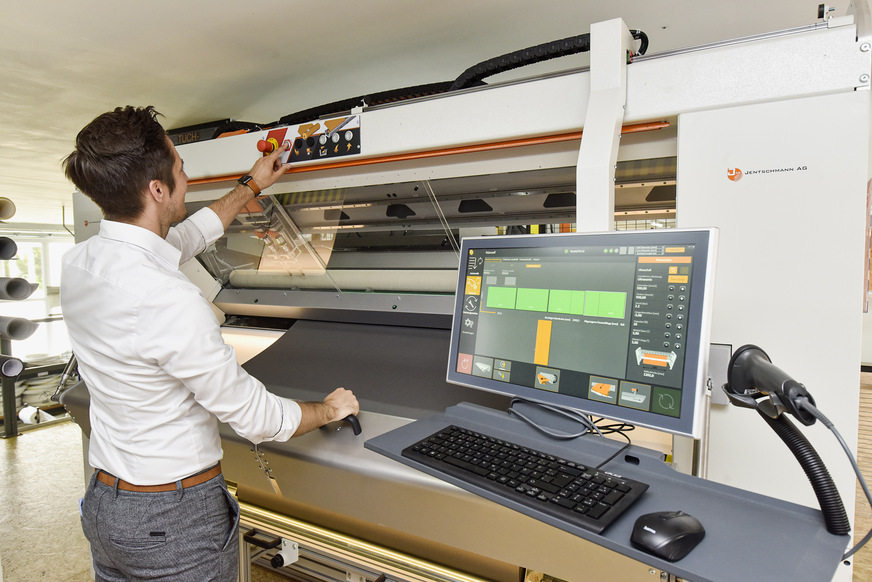
Foto: Mobau Markisen
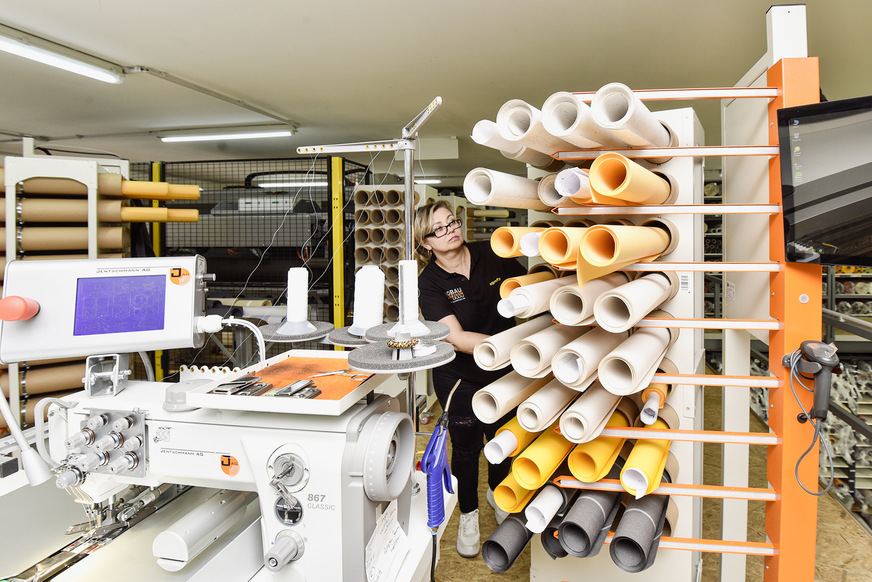
Foto: Mobau Markisen
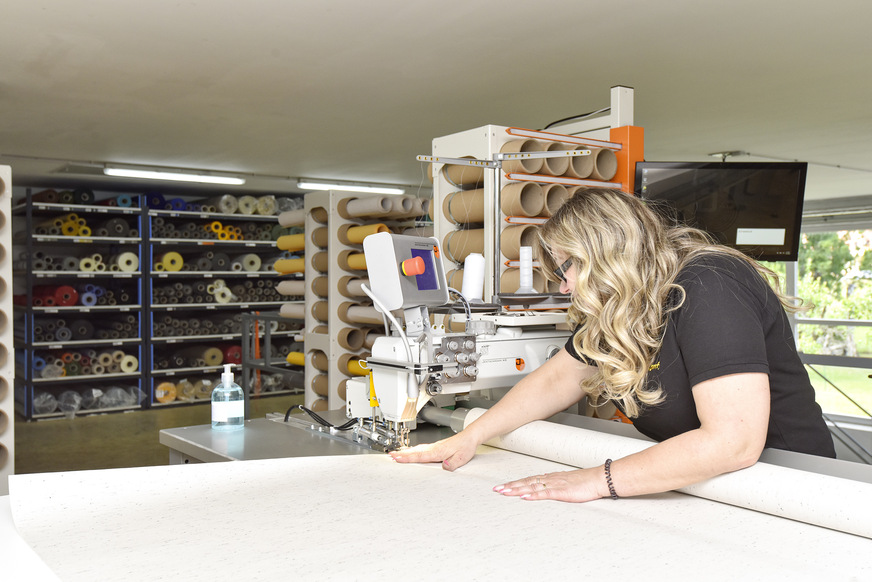
Foto: Mobau Markisen
Ein guter Überblick im Betrieb ist alles
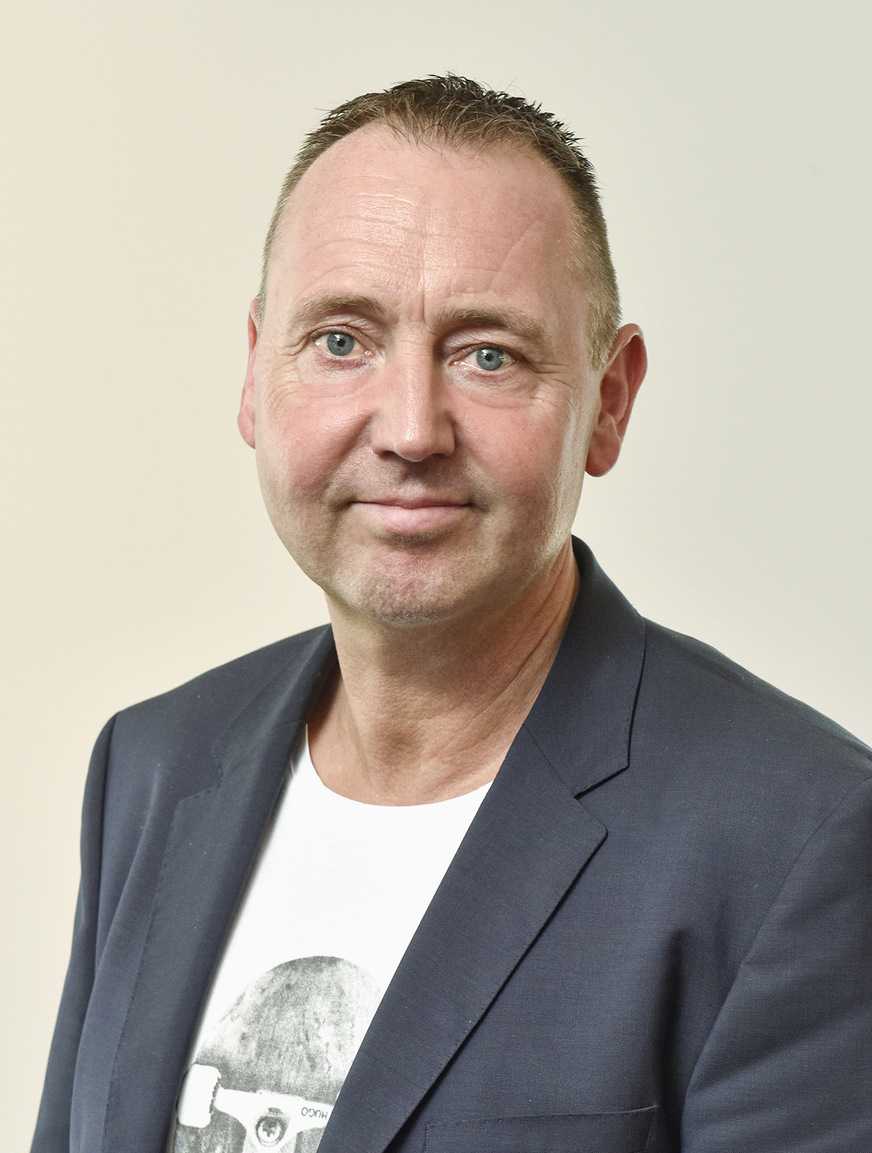
Foto: Marcel Discher
Die Erweiterung der Betriebsstätte wurde vom Europäischen Fonds für regionale Entwicklung gefördert. Die Redaktion der GLASWELT hat nachgefragt, worum es da geht.
GLASWELT – Man sagt Platz ist in der kleinsten Hütte. Konnten Sie ihr Ziel zu optimieren erreichen?
Marcel Discher – Ein klares Ja, wir haben unser Ziel erreicht. Es wurde eine Produktionssteigerung von über 50% erreicht und damit der Einsatz von Fremdleistungen reduziert.
GLASWELT – Sie nähen, was ist mit Kleben?
Discher – Wir haben uns an unserem Standort in Melsungen ganz klar für das Nähen entschieden, um unsere Kapazitäten besser planen zu können. Geklebte Tücher beziehen wir bei unserem Geschäftspartner Musculus. Wir können also beides in hoher Qualität liefern.
GLASWELT – Papierlose Produktion, was tut sich da bei Mobau?
Discher – Wir sind dabei ein neues ERP-System im Unternehmen einzuführen. Aber Step by Step, um sichere Abläufe zu schaffen. Eine Anbindung der Konfektion ist in naher Zukunft geplant und soll dann auch papierlos realisiert werden.