„Im Kern ist es ganz einfach, wir wollen zufriedene Kunden“, so Ralf M. Kronenberg gegenüber der GLASWELT beim Besuch am Standort Haan. „Wir fertigen Massenprodukte, die jeder Isolierglas-Hersteller in großen Mengen benötigt. Um in diesem Markt erfolgreich zu sein, müssen wir den Kunden – neben Produktinnovationen, Know-How und vielseitigen Produkteigenschaften – nicht nur eine hohe Produkt-Qualität gewährleisten, sondern diese Produkte auch mit höchster Liefertreue bereitstellen. Gleichzeitig müssen wir als Hersteller eine entsprechende Performance generieren, um unsere Produkte effizient und wirtschaftlich zu fertigen, damit wir wettbewerbsfähig bleiben. Und der Wettbewerb ist hart.“
Ähnlich geht es den Kunden von EK, den Isolierglas-Herstellern. Auch für sie spielt die Liefertreue eine entscheidende Rolle. Damit sie effizient und termingerecht ihre Isolierglas-Produkte herstellen können, müssen dazu alle Zulieferprodukte rechtzeitig vorliegen. Stockt es bei den Zulieferern, hat der Glasverarbeiter ein Problem.
Kronenberg: „Nach unserer jahrzehntelangen Erfahrung werden wir als Zulieferer und Partner vor allem an der pünktlichen Lieferung gemessen. Wobei eine hohe Produktqualität vorausgesetzt wird. Also haben für uns Termin- und Liefertreue die höchste Priorität. Im Rahmen der zunehmenden Digitalisierung unseres Unternehmens, richten wir die entsprechenden Maßnahmen nach dem Ziel aus, immer pünktlich zu liefern.“
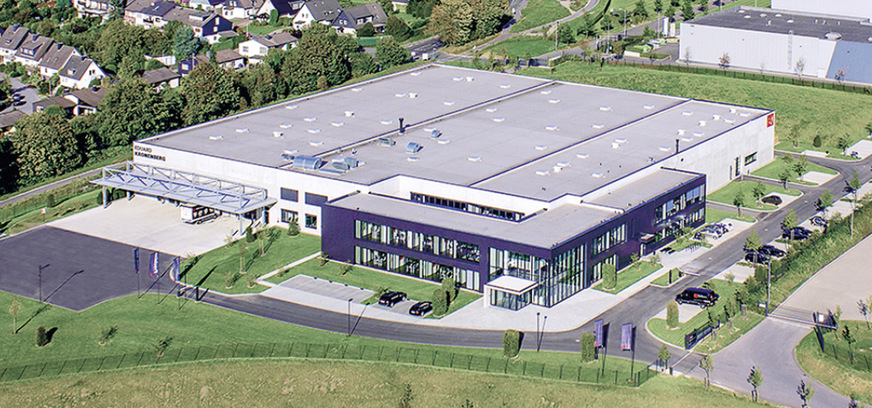
Foto: Knoche Werbung GmbH, Solingen
Der erste Schritt bei der Digitalisierung
Welche Schritte bei EK unternommen wurden, erläutert Digitalisierungsexperte Jörg Lichtenberg, der Operational Excellence Manager des Unternehmens: „Der erste Schritt im Rahmen der Digitalisierung des eigenen Betriebs liegt darin, ein oder mehrere Ziele zu definieren, die man mit seinen Maßnahmen erreichen will. Erst wenn diese Ziele auch wirklich klar definiert sind, kann man die Digitalisierung praktisch in Angriff nehmen.“ Und er ergänzt: „Früher haben sich die Betriebe eine neue Maschine angeschafft, wenn sie die Kapazitäten erhöhen wollten. Im Rahmen der Digitalisierung und Vernetzung eines Unternehmens reicht das nicht mehr aus. Heute muss jede Abteilung eingebunden werden, mit all ihren Anlagen sowie allen Mitarbeitern. Ein Betrieb kann nur dann optimal laufen, wenn alles, und ich meine alles, mit eingebunden ist.“ Das werde häufig nicht bedacht.
Ein effektiv digitalisierter Betrieb sei zudem transparent, und zwar an jeder Stelle, inklusive der Mitarbeiter. Jörg Lichtenberg unterstreicht: „Deshalb ist es wichtig, dass die Mitarbeiter dieses akzeptieren und vor allem auch mittragen und aktiv unterstützen.“
„Wie lässt sich die Performance bei Liefertreue und Effizienz steigern, das war bei uns die Fragestellung“, so Lichtenberg weiter. Insbesondere vor dem Hintergrund, dass das Unternehmen in beiden Punkten schon über eine sehr gute Performance sowie eine hohe Produktqualität im Rahmen einer hohen Liefertreue verfügt?
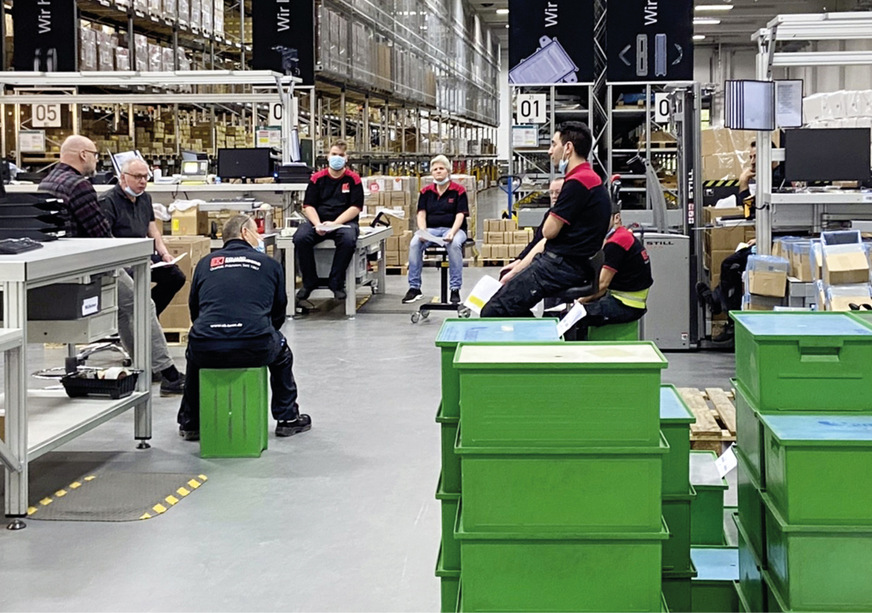
Foto: Matthias Rehberger / GLASWELT
Vielleicht stellt sich dem einen oder anderen nun die Frage: „Wenn das eh schon gegeben ist, warum das noch weiter steigern?
Ralf M. Kronenberg unterstreicht: „Einerseits dürfen wir nicht stehen bleiben und zum anderen soll und muss die Basis geschaffen werden, damit wir uns auch in den kommenden Jahren in einem hart umkämpften Markt erfolgreich positionieren können.“
Nur so lasse sich das Familienunternehmen auch für die Zukunft fit halten. Ganz nach dem Motto: Gutes immer besser machen. Ralf M. Kronenberg fasst zusammen: „Unser Ziel ist es, die Anpassungsfähigkeit unseres Unternehmens an zukünftige Herausforderungen stetig zu erhöhen.“
Dass mit Digitalisierungsexperte Jörg Lichtenberg der richtige Mann mit ins Team geholt wurde, belegt u. a. seine jahrzehntelange Erfahrung im Segment Supply Chain.
„Mein gesamtes Berufsleben konzentriere ich mich auf die Neuausrichtung und Optimierung der Supply Chain (auch international)“, so Lichtenberg. „Dabei war ich weltweit bei verschiedenen Unternehmen beschäftigt, unter anderem bei Dorma und später nochmals bei dormakaba. Was mich bei EK besonders freut ist die schnelle Umsetzung. Am EK Standort in Haan bin ich als Ingenieur nicht nur mit der Planung betraut, sondern auch mit der Umsetzung. Zu sehen, wie schnell die Umsetzung hier erfolgt und wie gut die Ergebnisse bei unserem Digitalisierungs-Projekt sind, das ist eine Freude.“
Maßnahmen zur Digitalisierung
Welche praktischen Schritte dann im Unternehmen unternommen wurden, erläutert der Digitalexperte: „Unser Ziel bei der Digitalisierung ist die Kundenzufriedenheit. Diese wird meist über die Liefertreue gemessen. Das ist einer, wenn nicht der wichtigste Gradmesser der Kundenzufriedenheit. Und wenn wir von Liefertreue sprechen, meinen wir kundenorientierte Liefertreue. Also maßgeschneidert für jeden einzelnen Kunden.“ Um die Lieferzuverlässigkeit noch weiter zu steigern, wurde das Performance-Programm OTD/OEE initiiert. Nach der Einbindung der verantwortlichen EK Team-Coaches sowie der Information aller Mitarbeiter über die Ziele dieses Performance-Programmes erfolgte dann im Januar 2021 der Programmstart.
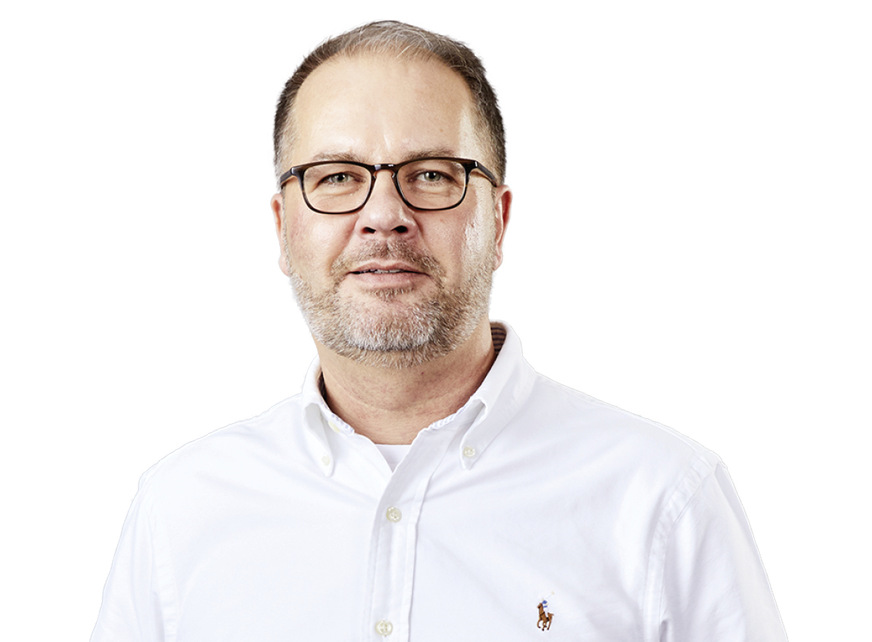
Foto: Dirk Schumacher, BFF Solingen
Zu Beginn wurde die Bedeutung der Kennzahlen von OTD (On Time Delivery) und von OEE (Overall Equipment Effectiveness) für die Leistungsbewertung von Unternehmen erklärt.
Hintergrund: Generell werden die Liefertreue und die Qualität maßgeblich von der Planung und deren effektiver Umsetzung in der Produktion bestimmt.
Jörg Lichtenberg: „Weil die Maschinenverfügbarkeit, Maschineneffizienz und der Qualitätsfaktor sowohl die Lieferzuverlässigkeit als auch die Produktionsqualität beeinflussen, werden bei uns im Betrieb diese drei Kriterien zur Bestimmung der relevanten Kennzahlen herangezogen.“
Die Optimierung berücksichtigt die Intern overall equipment efficiency. Das heißt die Anlagen-Verfügbarkeit im Verhältnis zur Produktionszeit, unter Einbeziehung der Leistung, Verfügbarkeit der Materialien und der Qualität. Es muss dabei hinsichtlich all dieser Punkte optimiert werden. Und hierfür werden Kennzahlen benötigt, die dies abbilden.
Die Haupteinflussfaktoren für die gewünschte Steigerung der Performance bei EK liegen konkret in der Verkürzung der Rüstvorgänge und einer Senkung der Werkzeugnacharbeiten der Stanzwerkzeuge und Formen für die EK-Produkte. Flankierend wurden die weitere Optimierung der Hubzahl, eine Flexibilisierung bei der Maschinenbelegung sowie eine Stärkung der Organisation im Ressourcen-Management ins laufende Projekt eingesteuert.
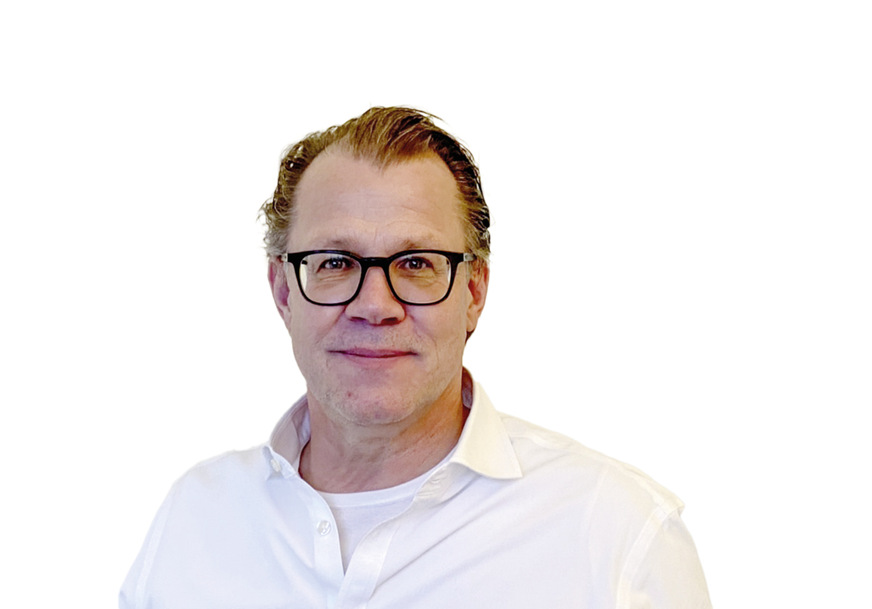
Foto: Matthias Rehberger / GLASWELT
Das Projekt entwickelt sich gut
Einen ersten Zwischenbericht über erreichte Ziele gab es im Mai 2021. Darin wurden u. a. die effektiven und neu etablierten Kommunikationsmaßnahmen aufgeführt – wie etwa Teamboards in der Logistik und in der Produktion, um schnell und direkt über die aktuellen Kennzahlen zu informieren – sowie die neu eingeführten täglichen Produktionsmeetings.
Ralf M. Kronenberg, der das Performance-Programm OTD/OEE eng begleitet, ist mit dem Fortschritt der Maßnahmen zufrieden: „Alle relevanten Kennzahlen weisen ausnahmslos in die richtige Richtung. Mein Dank dafür geht an unsere Mitarbeiter, die hoch motiviert mitziehen, sowie an die verantwortlichen Team- und Projektleiter. Wir werden diesen positiven Trend in den nächsten Monaten weiter systematisch vorantreiben.“
Wie sieht der Prozess bei einem Kundenauftrag aus?
Der Kunde macht seine Bestellung, diese wird dann in das ERP-System übertragen. Danach erfolgt die Planung für die Produktfertigung und anschließend die Erstellung der Produktionspläne (Maschinen, Werkzeuge, Mitarbeiter, Materialien).
Da die Maschinen komplett vernetzt sind, lässt sich der Auftragsprozess über alle Stationen hinweg komplett transparent darstellen, inklusive der zugehörigen Maschinenparameter etc. Diese werden über eine Vielzahl an Sensoren direkt von den Maschinen geliefert.
Die Daten stehen nun der Produktionsleitung jederzeit zur Verfügung und werden bei EK entsprechend ausgewertet und lassen sich bei Bedarf im laufenden Prozess jederzeit anpassen. Dabei hat jede Material-Charge eine eigene Kennzahl, dazu kommen die Werkzeugdaten (teils digitalisiert). Entsprechend des Auftragsablaufs wird das Werkzeug (Parameter und Maschinendaten) dann eingerichtet.
Digitalisierungsexperte Lichtenberg: „Die Herausforderung ist immer, die vorhandenen Daten sichtbar zu machen, auszuwerten und entsprechende Entscheidungen zu treffen, z. B. in welcher Losgröße produziere ich den nächsten Artikel, wann führe ich eine Wartung durch, nutze ich Werkzeug A oder B. Weiter haben wir ein Feinplanungs-Tool in das ERP eingebaut, das grafisch den Auftrag darstellt. Aus dem ERP lesen wir die Maschinendaten aus und bewerten sie, um Verfügbarkeit (Ausfallzeiten), Leistung (Hubzahl, Geschwindigkeit optimieren) und die Qualität der Produkte zu verbessern.
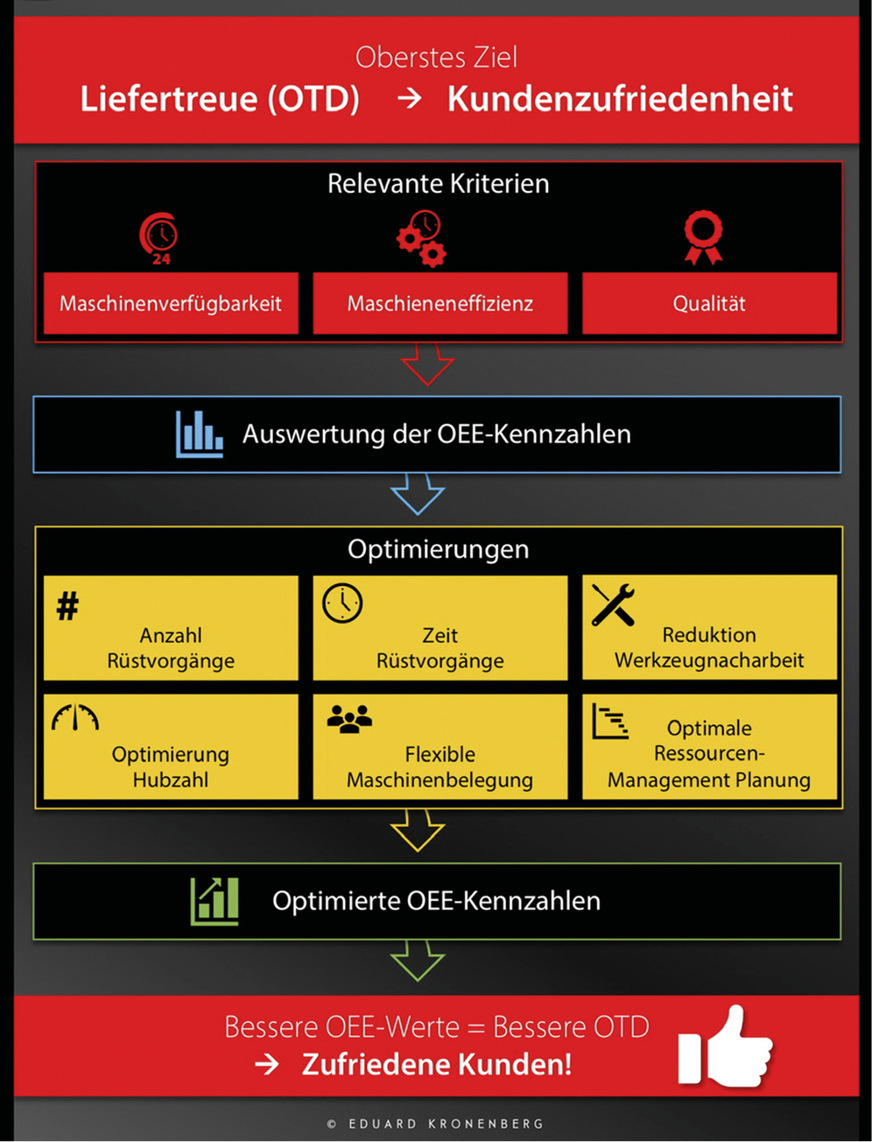
Foto: Eduard Kronenberg
Welche Rolle spielt der Einsatz von AI?
Man muss von Anfang an versuchen, so viele Daten wie möglich zu nutzen, um eine Optimierung der Produktion anzugehen, denn der Betriebsablauf wird von der Auswertung der vorhandenen Daten getragen.
Hierbei kommt bei EK künstliche Intelligenz (AI = Artifical Intelligence) zum Einsatz: „Mit AI arbeiten wir daran Muster zu erkennen, um Fehler zu finden und zu minimieren“, erläutert Jörg Lichtenberg. Da es sich um hoch komplexe Prozesse handelt, bei denen so viele Daten anfallen, braucht es AI, denn die Auswertung dieser Datenmengen kann ein Mensch nicht leisten.
Nach der Analyse der Maschinen, Werkzeuge und Materialdaten kommen bei der Analyse der Performance jetzt noch die Mitarbeiter (z. B. Maschinenbediener) dazu. Denn trotz automatisierter Prozesse braucht es den Input der Mitarbeiter. Lichtenberg: „Wie schaffe ich es, die Mitarbeiter zu motivieren und ihnen das Selbstvertrauen zu geben, eigene Entscheidungen zu treffen? Wenn ich das erreiche, bin ich der Optimierung meines Betriebs schon viel näher gekommen. Unsere Verbesserungsmaßnahmen haben wir im Führungskreis in Workshops diskutiert und entwickelt und dann überlegt, wie wir das mit den Mitarbeitern umsetzen. Meine Aufgabe war es von diesen zu erfahren, was man bei den speziellen Punkten im Unternehmen besser machen kann, um unser Hauptziel, eine Verbesserung der Liefertreue, zu erreichen.“ Lichtenberg unterstreicht: „Das Know-how und der Ausbildungsstand der Mitarbeiter ist in hohem Maß für die Produktqualität mit verantwortlich. Deshalb darf man nie die Mitarbeiter vergessen. Ohne sie läuft es nicht.“
Eine wichtige Fragestellung lautete: „Wie kann ich die Digitalisierung nutzen, um den Ausbildungsstand meiner Mitarbeiter zu verbessern?“
Jörg Lichtenberg: „Wir haben dann Projekte gesucht, wo der Human-Aspekt betrachtet wird und sind dann auf das Projekt AgiloLab der Universität Wuppertal unter Leitung von Prof. Dr. Stefan Diestel gestoßen. Nun sind wir dort Partner.“ Dieses Projekt untersucht, wie sich die Organisationsstrukturen in KMU besser gestalten lassen, auch mithilfe digitalen Lernens, um innovationsförderliche Arbeits- und Kooperationsweisen im Unternehmen zu implementieren. Die Führungsmannschaft von EK ist mit den Ergebnissen des Digitalisierungsprojekts sehr zufrieden. Doch die Optimierung bei der Eduard Kronenberg GmbH geht weiter.
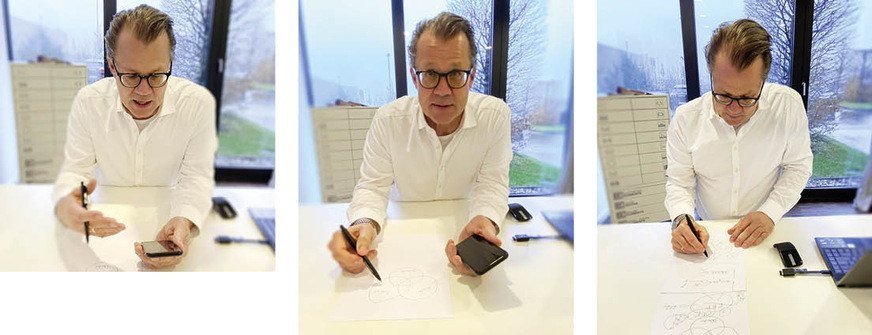
Fotos: Matthias Rehberger / GLASWELT