Die Anforderungen an die visuelle Qualität sind detailliert in der „Richtlinie zur Beurteilung der visuellen Qualität von Glas für das Bauwesen“ beschrieben. Üblicherweise ziehen ISO-Hersteller diese Richtlinie auch heran, um die Produktqualität der Gläser zu beschreiben. Aber wie sieht die Alltagspraxis aus? Kunden reklamieren oft Fehler, die deutlich kleiner sind, als in den Vorgaben definiert. Der Produzent muss häufig – trotz erfüllter Qualitätsrichtlinie – Ersatz liefern, will er keine Kunden verlieren. Obwohl es sich bei Reklamationen meist nur um einen geringen Anteil von rund 1Prozent an der Gesamtproduktion handelt und die Kosten dafür im Einzelfall mit durchschnittlich 50 bis 70 Euro/Einheit sehr gering sind, summiert sich übers Jahr gerechnet schnell ein Betrag in den Zehntausendern. Bei der ISO-Fertigung verlassen sich die meisten Betriebe fast ausschließlich auf die manuelle Kontrolle der Scheiben. Das ist kostspielig und die Zuverlässigkeit ist dabei nicht immer gewährleistet.
Effektive Kontrolle ein Muss
Der Einsatz von Scannern in Kombination mit digitaler Bildverarbeitung ist heute in der Lage solche Kontrollaufgaben mit überzeugenden Resultaten zu automatisieren und gleichzeitig manuelle Kontrollen abzulösen.
Eine wesentliche Voraussetzung ist, dass bei automatisierten, visuellen Kontrollsystemen zu bestimmten Fehlern, z.B. Kratzern, Blasen, Schmutz,…, eine zulässige Fehlergröße und Fehleranzahl exakt vorgegeben werden kann. Weiter muss es möglich sein, das Ergebnis der automatischen Kontrolle gezielt über einen Monitor mit dem Glas selbst vergleichen zu können. Nur so werden die Resultate transparent. Dazu darf das Prüfsystem keine Produktivitätseinbußen bringen und muss folgende Forderungen erfüllen:
- Handhaben unterschiedlicher Fertigungsgeschwindigkeiten bis 50 m/min
- Automatische Erkennung von Glasgrößen und Modellen
- Kein Einfluss der Beschichtung auf die Kontrollergebnisse
- Unempfindlich gegen Industrieumgebung mit Schmutz, Staub, …
Dazu kommt die Forderung aus der Praxis nach einer Qualitätsprüfung, die sich im Detail an unterschiedliche Kunden oder Glasarten anpassen lässt. Das heißt, dass man beispielsweise für einen privaten Haushalt strengere Qualitätsvorgaben einsetzen kann, als dies für eine öffentliche Einrichtung notwendig ist. Oder, dass VSG und ESG-Scheiben toleranter geprüft werden, als ein Standard Floatglas.
Mit dem Quality-Scanner-IG von Viprotron steht jetzt ein flexibles, automatisches Qualitäts-Kontrollsystem zur Verfügung, in das diese Forderungen erfolgreich integriert wurden. Über intelligente CCD-Kameras der neuesten Generation und einer intuitiven Windows basierten Bedienoberfläche, übernimmt der Scanner zuverlässig die Überwachung der Glasqualität innerhalb der Isolierglasfertigung. Das System ermöglicht es dem Isolierglasproduzenten, unabhängig von Personalmotivation und Schicht, eine gleich bleibende und reproduzierbare Glasqualität zu garantieren. Zusätzlich erfolgt eine detaillierte Dokumentation und Archivierung der Qualität, sodass der ISO-Hersteller auch noch nach Monaten die exakten Prüfergebnisse zu einer bestimmten Glaseinheit abrufen und ausdrucken kann.
Der nach der Waschmaschine vollständig in die Fertigungslinie integrierte Quality-Scanner-IG scannt die einzelnen Glasscheiben bei jeder Transportgeschwindigkeit – bis zu 50 m/min und mehr – und lokalisiert dabei die Fehler auf dem Glas. Die Fehler werden in Echtzeit typisiert und durch Vergleich mit den geforderten Qualitätsvorgaben erfolgt die Gut/Schlecht-Bewertung für das Glas. Ohne Produktivitätseinbußen werden fehlerhafte Gläser gemeldet oder gestoppt. Die Ergebnisse zu den einzelnen Gläsern können an beliebiger Stelle innerhalb der Fertigungslinie auf einem Monitor visualisiert werden. Dabei werden die Fehler – mit typabhängigen Symbolen – an den präzise errechneten Positionen auf der Glasscheibe dargestellt. So erhält der Anlagenbediener am Bildschirm nicht nur die Auskunft, dass sich ein Fehler auf dem Glas befindet, sondern er erkennt sofort anhand des Symbols, um welchen Fehlertypen es sich handelt und wo dieser liegt.
Das Scanner-System erkennt sicher alle visuell sichtbaren Defekte wie z.B. Blasen, Kratzer, Beschichtungs- und Folienfehler Zinn, Schmutz, Fingerabdrücke, etc. ab einer Größe von 0,5 mm2. Gleichzeit hat es der ISO-Produzent in der Hand, exakt zu definieren, welche Fehlertypen ab welcher Größe und Anzahl dazu führen, dass ein Glas als schlecht eingestuft wird.
Auch eine Unterscheidung nach dem Fehlerort (Falz-, Rand- und Hauptzone) wurde in das System integriert. Dazu steht zur Auswahl der gewünschten Qualität die menügeführte Windows-Oberfläche, die sich in Ihren Parametrierungsmöglichkeiten an der „Richtlinie zur Beurteilung der visuellen Qualität von Glas für das Bauwesen“ anlehnt.
Über eine Netzwerkkopplung und den zugehörigen Software-Interfaces kommunizieren der Scanner und das jeweilige Produktionsplanungs-System problemlos miteinander. So werden wichtige Daten aus den jeweiligen Datenbanken gegenseitig zur Verfügung gestellt. Entsprechende Anbindungen wurden bereits erfolgreich realisiert (z.B. an A+W-Systemen).
Damit die Wirtschaftlichkeit stimmt
Durch den Einsatz von modernen Scannersystemen lassen sich heute teuere Kundenreklamationen reduzieren und gleichzeitig Qualitätsverbesserung erzielen. Daneben kann das Kontrollpersonal deutlich entlastet oder mit anderen Aufgaben betraut werden. Durch das verzögerungsfreie bereitstellen der Inspektionsergebnisse lässt sich sogar eine Steigerung der Produktivität erreichen.
Durch eine intensive Auswertung der gespeicherten Inspektionsdaten sind auch Optimierungen in vorgelagerten Produktionsschritten wie dem Zuschnitt und dem Glashandling bis hin zum Einkauf des Glases möglich. Dazu werden neben der detaillierten Dokumentation und Statistik von Viprotron weitere Optionen angeboten, die den ISO-Hersteller darin unterstützen, die Produktivität mittels Quality-Scanner-IG zu verbessern.—
Mit dem Scanner lässt sich viel Geld sparen
Rechenbeispiel auf der Grundlage einer Fertigung von 80 ISO-Enheiten/Std. im Einschichtbetrieb (7,5 Std./Schicht), gerechnet auf 230 Arbeitstage/Jahr.
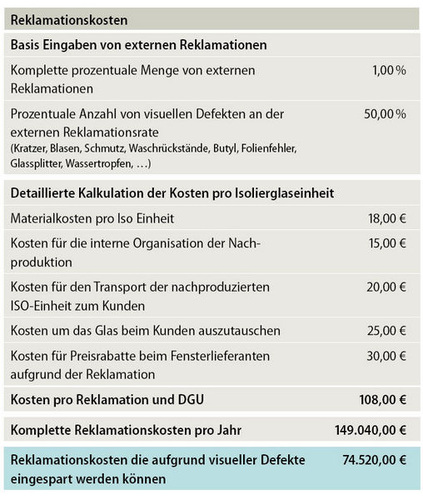