Leo Löffler hat viel Besuch bekommen von Kollegen aus dem Markt in den letzten Monaten. Das Who is Who der Fensterbranche hat sich in den Produktionshallen des Kunststofffenster-Herstellers in Kleinwallstadt eingefunden. Einen Blick werfen wollten dabei alle auf SVEN und die Prozesse, die dahinterstecken. SVEN ist der von der Firma Rotox entwickelte Glaskleberoboter, der seit Anfang 2020 fest in die Prozesse bei Löwe integriert ist. Der Name SVEN kommt nicht von irgendwo: „Unsere Produktionsleitung hat mich in der Anfangszeit zur GKA (= GlasKlebeAnlage, Anm. d. Red.) gerufen. Das hat mir nicht gefallen, das Kind braucht einen Namen dachte ich. Nach kurzen Überlegungen bin ich auf SVEN gekommen, das steht für die Eigenschaften, die wir durch die Verklebung erzielen: Sicher, Verklebt, Energieeffizient, Nachhaltig.“, so Leo Löffler.
Dass verklebte Fensterelemente besonders sicher und auch energieeffizient sind, hat sich in der Branche schon lange herumgesprochen. Schließlich wissen Experten, dass einerseits dem Einbrecher die Glasanbindung an den Flügelrahmen noch mehr Kopfzerbrechen bereitet und andererseits eine geklebte Verbindung der Konstruktion generell viel Stabilität verleiht, sodass – aktuell zumindest bei weißen Fenstern bis 1,4 m Stahllänge – auf ebendiese Stahleinlagen verzichtet werden kann. Das wiederum sorgt nicht nur für bessere U-Werte für das Fensterprofil, sondern auch für eine langfristige Kostenersparnis. Aber warum ist dieses spezielle Klebeverfahren besonders nachhaltig?
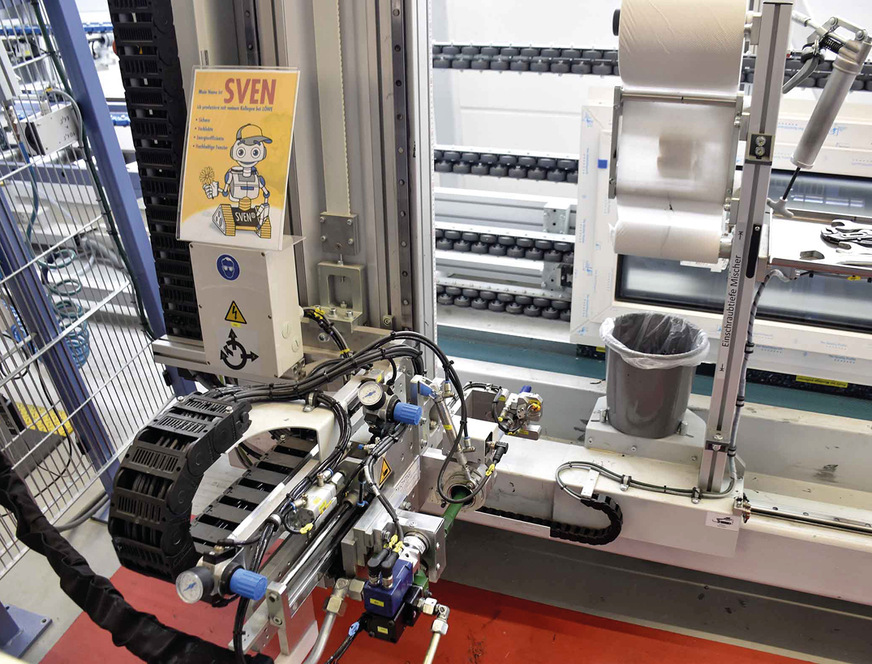
Foto: Daniel Mund / GLASWELT
Nachhaltiges Klebeverfahren entwickelt
Löffler hat sich mit den Abläufen und der Integration der Klebetechnik in die Produktionsmatrix intensiv beschäftigt und kann deshalb mit Fug und Recht behaupten, jetzt ein besonders nachhaltiges Klebeverfahren implementiert zu haben. „Wir haben insgesamt drei Jahre lang Erfahrungen gesammelt und dabei unwahrscheinlich viel Hirnschmalz, Zeit und Geld in diese Prozesse hineingesteckt.“ Es habe auch Rückschläge gegeben. „Aber am Ende ist etwas sehr Gutes dabei herausgekommen.“
Rückblende: 2017 hat Leo Löffler beim ift Rosenheim gemeinsam mit seinem ältesten Sohn Fabian einen Lehrgang zum RC2-Sicherheitsexperten absolviert. Es ging dann für ihn zunächst um die Frage, „wie wir die für den höheren Einbruchschutz notwendige Verklebung in unsere Produktion integrieren können.“ Im Anschluss daran sei ihm und dem Löwe-Team immer deutlicher geworden: „Ein verklebtes Fenster ist ein stabileres Fenster, das Qualitätsniveau steigt deutlich.“ Und mehr noch: Mit einem durchgängigen Klebeprozess lässt sich – anders als zunächst erwartet – auch noch wesentlich schneller produzieren, als mit der klassischen Verklotzung. „Das rutscht einfach schneller durch.“
Klebetechnik muss verstanden werden
Leo Löffler hat dabei für sich erkannt, dass die zentrale Prozess-Kompetenz innerhalb des Fertigungsbetriebes liegen muss: „Es kommt darauf an, alles unter einen Hut zu bekommen: Maschinen, Kleber, Prozesse. Und es gilt, die Technologie praxisnah selbst umzusetzen. Wir haben einen Profillieferanten, der ‚kleben kann‘, eine Maschine, mit der man ‚kleben kann, Kleber, der ‚klebt‘ und eine Scheibe, die ‚verklebt werden kann‘. Die Lieferanten untereinander tauschen sich wenig aus – beispielsweise aus welchen Materialien die Schläuche des Automaten sind. Dadurch hatten wir zu Beginn einige Probleme und mussten alle Vorlieferanten an einen Tisch holen, um gemeinsam ein funktionierendes System zu entwickeln. Das ist uns schlussendlich mit Hilfe von Rotox, Otto-Chemie, Maco und viel Eigeninitiative sehr gut gelungen, sodass wir nun stolz von uns behaupten können: Wir können richtig gut kleben!“
Daraus entstanden ist bei Löwe das Fenster mit dem Zusatz Hybrid-SV (Sicher Verklebt). Löffler ist überzeugt: „So bauen wir unser bisher perfektestes Fenster.“ Der hybride Ansatz dabei: Das Beste aus verschiedenen Welten zu vereinen: Ein Fenster ohne Stahl mit verklebter Fuge und die beste Verbindung von Scheibe und Flügel.
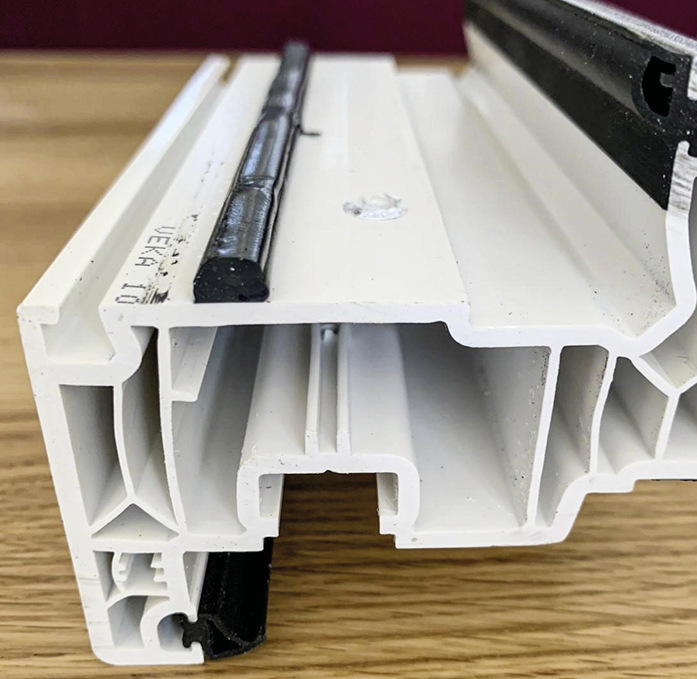
Foto: Löwe Fenster
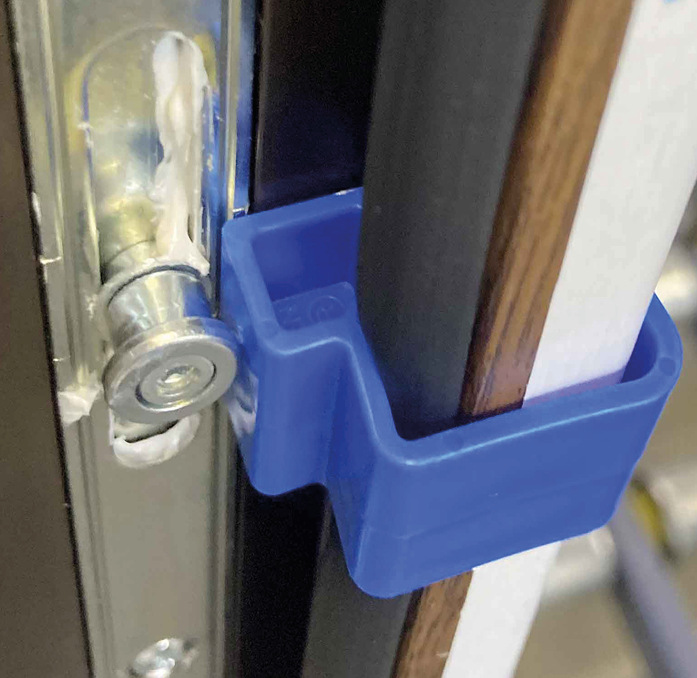
Foto: Daniel Mund / GLASWELT
Die Elemente können so umgehend verladen
werden.
Wozu dient der Klebekamm?
Wenn der Klebeprozess abgeschlossen ist, sind Korrekturen ausgeschlossen, der erste Anlauf muss also sitzen. Dazu hat Löffler das Verklotzungsprocedere ganz neu gedacht: In die Flügel werden die selbst entwickelten Flügelfalzklötzen platziert. Eine Verklotzung erfolgt nur an jenen Stellen, wo die Beschläge sitzen. Spezielle Stützklötze verhindern ein Absinken des Flügels im Dauergebrauch. Ist das Glas eingesetzt, fixieren Distanzklötze zwischen Flügel und Blendrahmen die Konstruktion beim Scherenlager und gegenüber.
Löffler geht ins Detail: „Da jeder Beschlag eine gewisse Toleranz in der Schere hat, wird über den Flügelfalzklotz die Toleranz ausgeglichen bzw. verringert. Wir sind – abweichend von den Empfehlungen Veka‘s – der Meinung, die Toleranzen im Beschlag mit einer Überklotzung von einem Millimeter auffangen zu können.“
Mit dem unmittelbar unter der Schere angesetzten blauen Distanzklotz wird das Spiel im Beschlag reduziert. So kann das Fenster umgehend nach dem Einschlagen der Glasleisten von der Fertigungslinie entnommen und auf Transportböcken abgesetzt werden. Damit aber dieser Distanzklotz vor dem Verkleben und nach der Montage auf der Baustelle nicht vergessen wird, hat Löffler ihn mit einer an der Flügelkante sichtbaren Lasche ausgestattet. Früher waren entsprechende Positionierungsklötze am geschlossenen Fenster nicht zu erkennen und wurden schon vor dem Verklebungsprozess oft vergessen. Diese Probleme hat Löffler damit im Griff.
Damit die Glasscheiben nach „Hochzeit“ exakt in Position gebracht werden, hat der Unternehmer selbst eigens dafür spezielle „Klebekämme“ sowie den dazugehörigen „Klebekammlöffler“ entwickelt. Mit ihrer Hilfe werden die Distanzklötze in Position gebracht.
Bei der Klotz-Positionierung wird auch die ganze Akribie im Prozess deutlich: Schon am Bearbeitungszentrum werden kleine Flügel-Markierungen gesetzt. So ist beim Verglasungsprozess klar ersichtlich, wo welcher Klotz positioniert werden muss. Im Übrigen lassen sich die speziell designten Distanzklötze auch dort platzieren, wo ein Beschlagszapfen sitzt, weil dieser hinter dem Klotz vorbeiläuft.
Insgesamt betrachtet glaubt Löffler, dass sich die Klebetechnik gerade deswegen noch nicht so breitflächig durchgesetzt hat, weil eben doch auf so viele Kleinigkeiten im Produktionsprozess geachtet werden muss. Es reicht eben nicht, sich auf seine Systempartner zu verlassen, man muss viele weitere Herausforderungen innerhalb der Produktion lösen.
Seit März 2020 hat er komplett umgestellt. „Wir verkleben möglichst durchgängig. 2021 waren es 98,3 Prozent aller Flügel.“ Der Prozess ist nun so reibungslos, dass die Anlage tatsächlich blockweise angefahren wird und so lediglich rund 70 Prozent am Tag genutzt wird. „Wir kleben also teilweise nur 5 bis 6 Stunden am Tag.“
Düsentechnologie weiterentwickelt
Ein weiteres Patent von Löffler betrifft den Vorgang des Einspritzens des Klebstoffes. Das Problem befindet sich nämlich ganz vorne an der Düse: Hier kommen die beiden Klebstoffkomponenten zusammen und werden durchmischt. Die teflonbeschichtete Stahldüse wird besonders durch die im Flüssigklebstoff befindlichen Rußpartikel – die dem Klebemedium auch seine charakteristische schwarze Farbe geben – beansprucht. „Das ist wie Schmirgelpapier“, erläutert Löffler. Die Folge ist ein hoher Verschleiß der Klebedüsen.
Wenn die Anlage dann für eine gewisse Zeit aussetzt (z. B. nach Schichtende), beginnt der Aushärtungsprozess in der Düse. Dieser Kleberest muss beim Restart zunächst aufwendig entfernt werden – Zahnstocher, Bohrer und Pfeifenreiniger sind beispielsweise gängige Hilfsmittel an Klebestationen vieler Fensterbauer. Die andere Möglichkeit: Nach dem Klebeeinsatz wird das Leitungssystem bis zur Düse mit der A-Komponente (Füller/Mischer) geflutet, die nicht aushärten kann. Allerdings verschwendet dieser Reinigungsmethode reichlich viel Klebstoffmaterial.
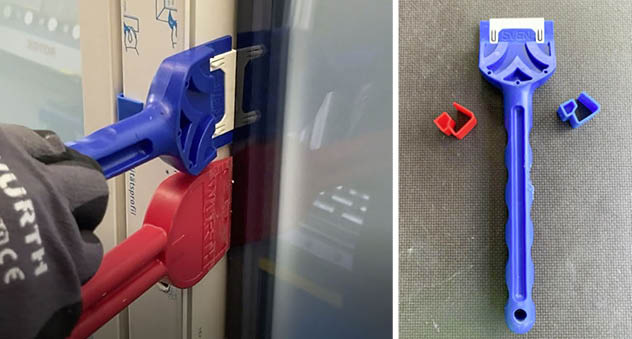
Foto links: Daniel Mund / GLASWELT; Foto rechts: Löwe Fenster
Materialeinsatz effizient genutzt
Der Tüftler wollte hier mehr erreichen: „Wir haben jetzt eine neue Düse mit Rotox patentiert, die drei Besonderheiten aufweist.“ Die Klebemenge selbst konnte auf die Hälfte reduziert werden, ohne Funktionseinbußen in Kauf nehmen zu müssen. „Wir verfügen jetzt mit 50 Prozent Materialeinsatz sogar über eine bessere Statik im Flügelprofil, bei einer ganz filigranen und kompakten Klebefuge. Und wir gehen mit der Düse direkt an die Scheibe und an das PVC.“
Gleichzeitig ging es Löffler darum, die Klebefugen-Farbe zu wechseln. Einerseits lässt sich damit die Klebefuge zur Qualitätskontrolle deutlicher von dem Randverbund des ISO-Paketes unterscheiden, andererseits lässt sich dann auch der Rußanteil im Kleber durch andere Farbpigmente substituieren. „Die Anfrage beim Zulieferer Otto-Chemie für den Zweikomponenten-Kleber S 670 wurde positiv bewertet und umgehend umgesetzt.“ Mit dem neuen hellgrauen Kleber konnte der Düsenverschleiß deutlich reduziert werden. Auch die ganze Anlagentechnik wie Zahnradpumpe und Leitungen werden nun wesentlich weniger stark beansprucht und verfügen demnach über eine höhere Lebenserwartung.
Spezielle Düsentechnik für RC2-Fenster
Als ein wichtiger Partner in der Weiterentwicklung erweist sich Beschlagslieferant Maco aus Salzburg: Auf seinen Prüfständen konnte Löffler bereits umfangreiche statische Festigkeitsprüfungen vornehmen und seine Fenster bis hin zur Einbruchsklasse RC2 testen. Dabei ist klar: Für das Erreichen einer erhöhten Einbruchsschutzklasse ist ein erhöhter Kleberauftrag vonnöten. Löffler: „95 Prozent der RC2-Fenster im Markt würden einem Einbruchstest sicher nicht bestehen“, weil genau hier nicht sauber gearbeitet werde.
Bei Löwe Fenster greift man bislang im RC2-Bereich zurück auf die Handapplikation. Aber künftig wird es auch hier mit SVEN ablaufen – dank spezieller Düsentechnik, die den erhöhten Klebebedarf bereitstellen soll und neu entwickeltem Düsenkopf. Sein Anspruch macht Löffler an dieser Stelle noch einmal deutlich: „Ich will alle unsere Produkte freigeprüft haben, zugleich soll der Prozess einwandfrei reproduzierbar sein.“ Diese reproduzierbaren Prozesse würden am ehesten mit der Klebetechnik und SVEN umzusetzen sein.
Dass in der Klebetechnik generell, speziell in der Klebedüse noch mehr Potenzial schlummert, liegt für Löffler auf der Hand: „Wir tüfteln weiter“. Mehr will er aber in diesem Punkt noch nicht verraten.
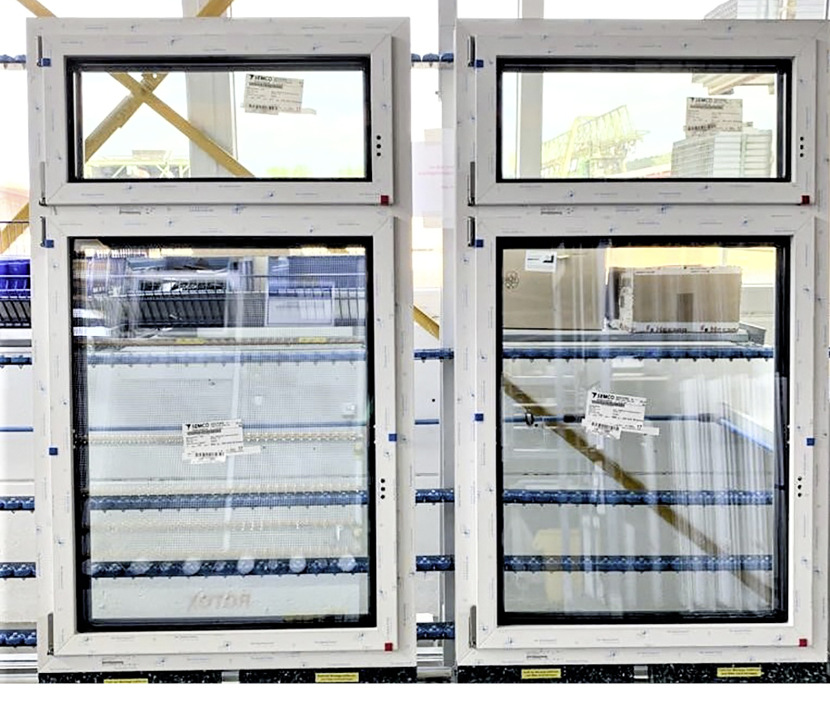
Foto: Löwe Fenster
Verglasungsklötze und Klebekämme
Die speziell für die Glasverklebung entwickelten Klebekämme als auch die Flügelfalzklötze mit spezieller Geometrie können über einen Vertriebspartner (Handelshaus Profipartner GmbH in Altenstadt) als Lizenzprodukte (europaweite Patente angemeldet) bezogen werden: www.ppv-profipartner.de
Löwe Fenster
Das Unternehmen in Kleinwallstadt mit seinen rund 75 Mitarbeiter produziert jährlich circa 10 000 Kunststofffenster und vertreibt diese auch selbstständig in der Ausstellung am Stammsitz in Kleinwallstadt und in einer weiteren Ausstellung in Rödermark. Die Montage wird selbst abgewickelt – oder an langjährig bekannte Subunternehmer vergeben.
Auf Nachfrage und angesichts der umfangreichen Entwicklungsschritte innerhalb der Produktion kann sich Leo Löffler jetzt auch als weiteren Absatzkanal den Vertrieb an Schreinerkollegen und an Wiederverkäufer vorstellen.