glaswelt – Was ist das Besondere an dem Unternehmen Beelitz Fensterbau?
Lisa-Marie Beelitz – Wir produzieren ausschließlich Brandschutzfenster aus Holz und Holz-Aluminium. Wir tummeln uns zudem auch im Einbruchschutz – meistens in Kombination mit dem Brandschutz.
GW – Wer sind Ihre Kunden?
Mike Beelitz– Hauptsächlich natürlich Tischler und Fensterhändler. Zu einem ganz kleinen Prozentsatz bedienen wir auch Endkunden direkt.
GW – Bei den Endkunden montieren Sie auch?
Mike Beelitz– Nein, wir montieren nicht. Jeder Kunde von uns muss die Montage selbst organisieren.
GW – Die Montage für Brandschutzfenster ist aber auch kein triviales Thema.
Mike Beelitz– Richtig, dafür liefern wir aber auch eine umfassende Montageanleitung mit. Jeder Schritt ist klar definiert. Für die Behörden geht es darum, dass der Montagebetrieb die Einhaltung der Anweisungen quittiert.
GW – Wie vielfältig sind die Wünsche Ihrer Kunden in Bezug auf die Gestaltung der Fenster?
Lisa-Marie Beelitz – Wir sind in Bezug auf die Kundenwünsche sehr flexibel, beispielsweise was die Oberflächen angeht bieten wir Applikationen von Remmers und Adler. Auch bei der Gläserwahl bieten wir ein breites Spektrum. Generell bewegen wir uns zwangsläufig im Rahmen unserer Prüfzeugnisse. Dabei können wir am Beschlag nicht viel ändern – wir sind im Übrigen aber auch sehr zufrieden mit unserem Beschlagshaus Maco.
Mike Beelitz – Unsere Fenster sind aufgrund unserer Profilgeometrie so schlank, dass der Kunde zum Teil ein normales Fenster nicht von einem Brandschutzfenster unterscheiden kann. Das gleiche gilt für unser Holz-Aluminium-Fenster. Hier arbeiten wir mit Stemeseder erfolgreich zusammen.
GW – Muss ein Brandschutzfenster immer in Eiche sein?
Mike Beelitz – Die Zeiten sind schon lange vorbei. Wir haben Prüfzeugnisse in der Rohdichte ab der Holzart Fichte und Kiefer.
GW – Wie viel Mitarbeiter arbeiten bei Beelitz?
Mike Beelitz– Wir sind ein Team mit 20 Mitarbeitern, davon sind 6 Auszubildende. 5 Mitarbeiter sind jetzt auf der Anlage geschult.
GW – Ihr habt aber eine imposante Ausbildungsquote! Keine Probleme, die jungen Menschen für sich zu gewinnen?
Lisa-Marie Beelitz – Natürlich ist das eine Herausforderung, immer genügend neue junge Leute für uns zu gewinnen. Aber wir machen dafür sehr viel: Ich bin Ausbildungs-Botschafterin für die Handwerkskammer, gehe in die Schulen rein und berichte von unserem tollen Job. Ich gehe zu Ausbildungsmessen und wir laden die Schulen zu uns ein. Unser Anspruch ist die volle Integration unserer Azubis. Die arbeiten an der Hobelbank und müssen nicht die Werkstatt fegen. Auch dürfen sie gleich in die Fertigung mit reinschauen und mitmachen. Nach der Ausbildung sind sie wirklich optimal für unsere Zwecke ausgebildet.
GW – Wie sind Sie in der Führungsebene aufgestellt?
Lisa-Marie Beelitz – Mein Vater hat den Betrieb 2013 gegründet. Er ist absoluter Experte, was die Fensterkonstruktionen im Brandschutz angeht. Ich bin seit drei Jahren im Unternehmen, seit letztem Jahr mit Prokura ausgestattet. Wir haben uns seit der Gründung immer mehr spezialisiert: Betrug der Anteil an Brandschutzverglasungen 2015 unter 10 Prozent vom Umsatz, so liegen wir jetzt bei über 95 Prozent.
GW – Welche Kriterien haben dazu geführt, dass Sie sich bei der Anlagentechnik für eine Biesse entschieden haben?
Lisa-Marie Beelitz – Wir sind bislang auch ohne CNC-Technik ganz gut ausgekommen. Zudem gab es kaum einen Maschinenanbieter, der sich mit unserem Portfolio auseinandersetzen wollte. Man muss beachten, dass unsere Brandschutzfenster konstruktionsbedingt eine hohe Bautiefe aufweisen – bis zu 135 mm. Da haben sich nicht viele herangetraut. Außerdem hatte mein Vater einige Ansprüche an die Anlagentechnik – wenn schon, dann sollte diese Maschine alles können, zumindest aber auch die Türenfertigung abdecken. Am Ende ist Biesse übriggeblieben.
GW – Wie haben Sie vorher Fenster produziert?
Mike Beelitz – Wir haben vorher mit einem stationären Fälzer und Zapfenschläger gearbeitet und uns zunächst nach traditionellem Maschinenersatz umgeschaut. Aber es gibt gar keine Neumaschinen mehr dafür. Deswegen schwenkte unser Blick auf die CNC-Technik – bis dato war ich eigentlich davon überzeugt, dass so eine Anlage für uns nicht in Frage kommt.
Lisa-Marie Beelitz – Dadurch, dass unser Team so fit ist, waren wir auch mit der klassischen Anlagentechnik sehr flexibel. Das Problem, womit wir uns trotzdem beschäftigen müssen, ist der Fachkräftemangel hier in Brandenburg. Dem wollten wir vorgreifen und unser jetziges Team mit einer guten CNC noch effizienter ausstatten.
GW – Herr Rauscher, gehört die Umstellung bei Beelitz bei Ihnen zum Standard-Repertoire?
Martin Rauscher – Ich habe keine Standard-Kunden. Das ist ja auch das große Glück für uns, dass es eben keinen Standard in der Werkzeugausstattung gibt. Wir wickeln jedes Projekt kundenspezifisch ab, jeder Kunde hat eine eigene Anforderung. Mit Beelitz haben wir natürlich einen absoluten Spezialisten mit einer starken Alleinstellung. Das freut uns sehr, denn nur die Herausforderungen bringen uns weiter. Die Profilgeometrien wurden von der Firma Beelitz vorgegeben, hier mussten wir nicht mehr in die Beratung reingehen. Nichtsdestotrotz haben wir auch in den Konstruktionsdetails weiter optimiert.
Florian Küch – Der Projektablauf wiederholt sich natürlich immer wieder. Da haben wir bereits eine gewisse Routine: Schulung, Aufbau und alles was sonst noch dazugehört. Alles andere als normal ist natürlich das Portfolio des Unternehmens und damit auch die Anforderungen an die Maschine, weil mit den großen Geometrien auch eine massive Spanabnahme verbunden ist. Da geht es vor allem um die Spindelleistung und die Absaugung. Durch den Vorab-Aufbau der Maschine bei uns in Nersingen wird aber schon viel im Vorfeld überprüft.
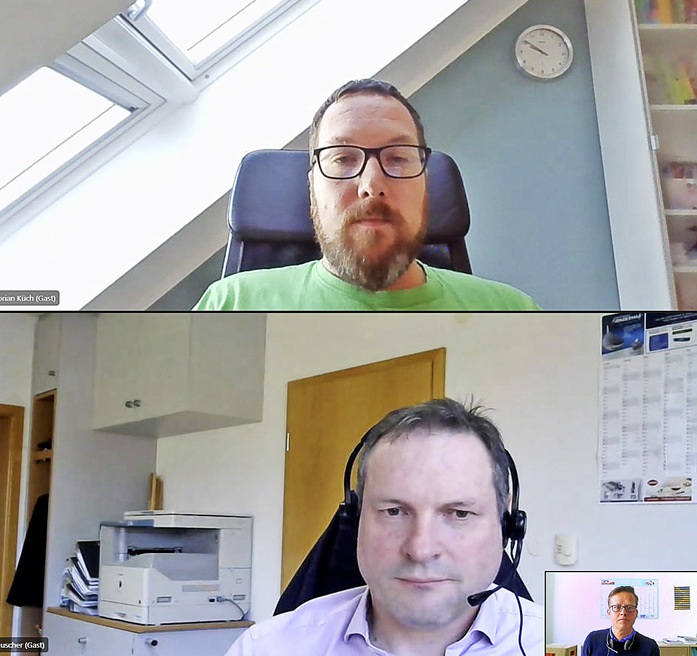
Foto: Daniel Mund / GW
GW – Was zeichnet denn die Biesse Winline als solche aus?
Florian Küch – Die Maschine ist für den Mittelstand konzipiert, ein Allrounder sozusagen. Wir konfigurieren für den Kunden beispielsweise die Spindelleistung und -anzahl. Bei Beelitz haben wir zwei 30 kW-Spindeln draufgepackt. Wir fahren mit zwei Aggregaten aufgrund der hohen Spanabnahme und der Fälze. Fällt eine Spindel aus, wird die andere aktiviert. Was die Winline ausmacht, ist die Flächenbearbeitung für Haustüren, auch Rundbögen sind hier möglich. Die Softwareansteuerung mit NC-Hops – ein freies Programmiersystem – bedeutet, dass sich auf dieser Maschine alles draufprogrammieren lässt, was eine normale CNC auch kann. Das macht die Anlage so einzigartig.
GW – Erläutern Sie bitte den Einsatz der NC-Hops-Software im Zusammenspiel mit der Fensterbausoftware Prologic.
Florian Küch – Die Fensterbausoftware kommt irgendwann auch an ihre Grenzen – wenn es in die Richtung Spitzbögen, Korbbögen oder ähnliches geht. Anwender bekommen eine DXF-Zeichnung vom Kunden und diese lässt sich per NC-Hops einlesen und dann frei programmieren auf den Anlagen.
GW – Wie lange hat es gedauert, bis Sie auf der Anlage verkaufsfähige Fenster produziert hatten?
Mike Beelitz – Wir mussten in der Werkstatt zunächst ein großes Fundament setzen. Das war schon mit erheblichem Aufwand verbunden. Am Wochenende bevor die Anlage angeliefert wurde haben wir unsere alten Maschinen rausgeschoben. In der zweiten Woche nach dem Aufbau haben wir dann schon erste Aufträge abgearbeitet.
GW – Wie groß war anfangs die Angst, etwas an der Anlage kaputt zu machen?
Mike Beelitz – Diese Angst haben wir unseren Mitarbeitern genommen, indem wir Ihnen mitgeteilt hatten, dass es eine Bruchversicherung gibt. Wenn etwas passiert wäre, dann wären wir trotzdem entspannt gewesen.
Lisa-Marie Beelitz – Mein Vater hatte von Anfang an großes Urvertrauen in die Anlage. Ich habe immer noch großen Respekt vor der Technik.
Martin Rauscher – Man hat als Außenstehender gleich erkannt, dass das Beelitz-Team wirklich weiß, was sie machen und was sie vorhaben.
Florian Küch – Unserer Meinung nach sind die zweiwöchigen Vorabschulungen bei uns in Nersingen von elementarer Bedeutung. Dadurch werden alle Projektbeteiligten viel entspannter. Der Kunde sieht sein Werkzeug, sein Holz, seine Maschine und seine XML-Daten. Dabei kann er abschätzen, wie es funktionieren wird und es entsteht das Vertrauen in das Projekt und die Beteiligten. Wir nehmen immer 12 Installationstage beim Kunden in Anspruch – aber auch hier konnte der Kunde schon ab Tag 8 seine Aufträge abarbeiten.
Mike Beelitz – Auch die Software-Umstellungen im Vorfeld ging ziemlich fix – besser als ich erwartet hatte. Obwohl zwischen beiden Software-Programmen Welten liegen. Eine Angebotserstellung darf bei uns nicht lange dauern, das konnten wir bestens umsetzen.
GW – Mit welcher Fensterbau-Software haben Sie in der Vergangenheit operiert?
Mike Beelitz – Wir hatten in der Vergangenheit mit Pinncalc auf Adulo-Basis gearbeitet – mit der CNC-Entscheidung haben wir dann bereits im Vorfeld auf Prologic umgestellt. Also schon deutlich vor dem Anlieferdatum der neuen Anlage. Jetzt arbeiten wir mit der Enterprise-Version von Prologic. Das bedeutet, dass unsere Händler selbst einen Account bekommen können und die Angebote selbst erstellen und die Fertigungslisten zur Maschine transferieren. In dem Fall müssen wir gar nicht mehr eingreifen.
Lisa-Marie Beelitz – Parallel haben wir auch unseren Online-Konfigurator hochgefahren, mit dem unsere Kunden ihre Brandschutzfenster selbst konfigurieren können. In der Regel ist es so: Jede Anfrage, die bei uns bis 15 Uhr eingeht, spiegeln wir dann bis 17 Uhr dem Kunden mit einem Angebot zurück. Wir können aber auch noch schneller: Wir haben schon Anfragen nach 5 Minuten beantwortet.
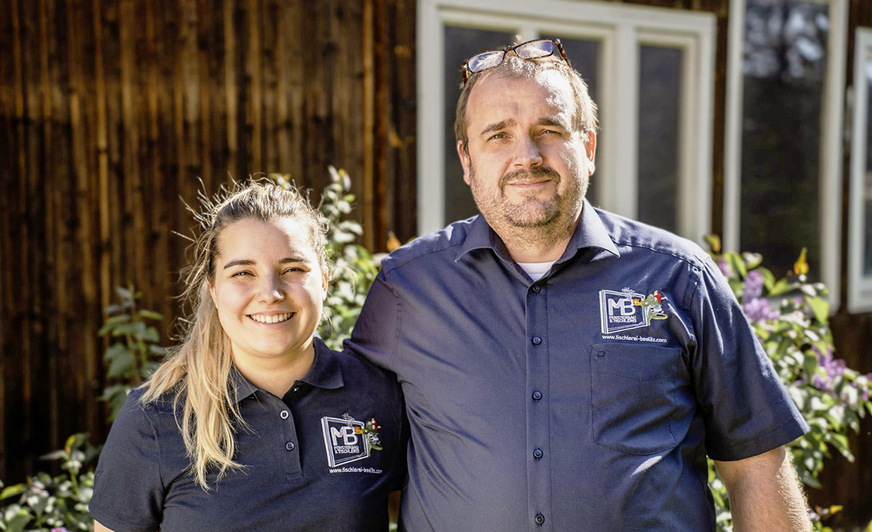
Foto: MB Fensterbau & Tischlerei e. K.
GW – Kommen wir auf das Werkzeug bei Ihnen im Hause zu sprechen.
Mike Beelitz – Zuani ist bei uns durch die CNC-Technik ein wichtiger Werkzeuglieferant geworden. Mit Martin Rauscher haben wir unser Werkzeugportfolio gemeinsam abgesteckt.
Martin Rauscher – In der CNC-Technik werden sehr viele Daten angefordert – sowohl maschinen- als auch softwareseitig. Dazu braucht man eine gewisse Erfahrung und die Performance in der Technik. Das bringen wir beides mit.
GW – Wie oft kommt das vor, dass Sie Fensterbauer unterstützen, die von der stationären Fensterfertigung umstellen auf die CNC-Technik?
Martin Rauscher – Über die Hälfte der Kunden hat bereits Erfahrung in der CNC-Technik, es findet bereits ein Generationenwechsel in der Anlagentechnik statt. Bei Neueinsteigern wie Beelitz, nehmen wir dem Kunden die Organisation ein Stück weit ab und das ist das, was man in diesem Fall auch braucht. Wenn man ein Team im Rücken weiß, das mit der Maschine, dem Werkzeug und der Software gut zusammenspielt, gelingt die Umstellung auch ohne Stress.
Florian Küch – Die projektbeteiligten Zulieferer müssen wissen, worauf es ankommt. Wir arbeiten schon viele Jahre zusammen mit Zuani und viele Winline-Anlagen sind mit Zuani bestückt – von daher bringen wir reichlich Know-how und Erfahrung in dieser Kombination mit.
GW – Gab es in der Belegschaft Vorbehalte gegenüber der CNC-Technik?
Mike Beelitz – Die Mitarbeiter mussten sich schon etwas umgewöhnen. Denn bereits in der AV muss alles passen, ansonsten kommt hinten Müll raus. Aber wir sind jetzt deutlich schneller als vorher.
Martin Rauscher – Das Unternehmen Beelitz hat jetzt in Sachen Qualität noch mal eine ordentliche Schippe draufgelegt. Die ganzen Bänder- und Taschenfräsungen werden jetzt am Rohholz gemacht. Früher wurden diese am profilierten Element gefräst, was zu Ausrissen geführt hat.
Mike Beelitz – Auch was die Oberflächenqualität angeht, haben wir uns deutlich gesteigert, können sogar den Zwischenschliff auslassen. Dafür geht es jetzt darum, die Werkzeuge wirklich rechtzeitig zu wechseln und nicht zu warten, bis es gar nicht mehr geht. Summa summarum bekommen wir eine bessere Oberfläche hin, bei einer viel kürzeren Durchlaufzeit.
GW – Es ist ja schon erstaunlich, dass Sie jetzt die Anlage rund sechs Wochen im Einsatz haben und bereits so begeistert sind von der Investition – als ehemaliger Verfechter der traditionellen Fertigungstechnik. Sind sie jetzt ein CNC-Technik-Fan?
Mike Beelitz – Ich will das so beantworten: Ich stell mich auch mal samstags hin, schmeiß die Maschine an und horche, ob noch alles im grünen Bereich ist. Ich sehe ja, dass uns die Anlage zu mehr Kapazität verholfen hat. Uns stehen jetzt mehr produktive Zeiten zur Verfügung. Die Anlage kann auch schon mal 3 bis 4 Stunden alleine schaffen. Anfangs standen wir noch daneben und haben andächtig zugeschaut, jetzt lässt man sie machen und widmet sich anderen Arbeiten. Man braucht auch nicht unbedingt die spezielle Fachkraft an der Anlage – theoretisch kann diese auch von einem angelernten Mitarbeiter bedient werden. Auch ein riesiger Vorteil: Die Ersatzbeschaffung eines Fensters gestaltet sich äußerst einfach. Da muss man nur die entsprechende Konfiguration anwählen, wenn wir ein Element nachbauen müssen. Früher war der Aufwand riesengroß.
Lisa-Marie Beelitz – Und wir können die jungen Mitarbeiter für die Technik begeistern. Wir haben beispielsweise unseren Auszubildenden aus dem ersten Lehrjahr mit zur Anwenderschulung als zertifizierter Maschinenbediener zur NC-Hops-Schulung geschickt. Der war tatsächlich auch derjenige, der die Technik am schnellsten umgesetzt hat.
GW – Das hört sich vielversprechend an! Ich wünsche noch viel Erfolg mit der Anlage.
Das Gespräch führte Chefredakteur Daniel Mund.
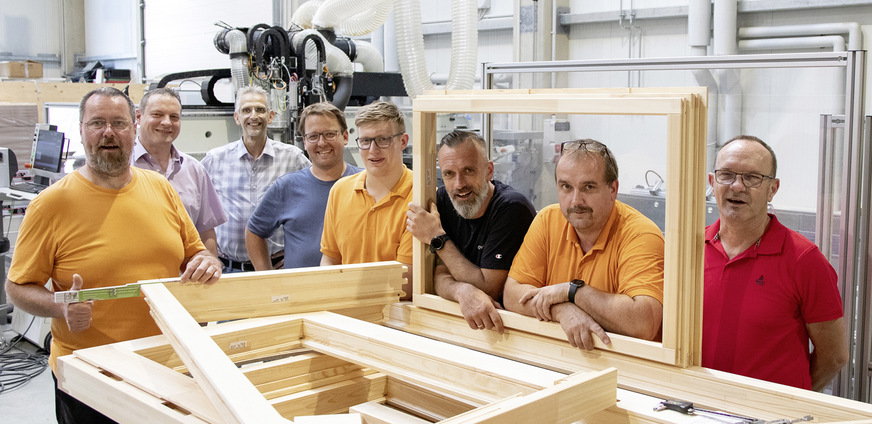
Foto: MB Fensterbau & Tischlerei e. K.