_ Interpane ist nicht nur Hersteller von übergroßen Scheiben, sondern auch einer der Pioniere in diesem Markt und fertigt seit 2012 sogenannte „Giga Lites“. Das sind Gläser bis 18 m Länge, die im Werk Plattling in einer der modernsten Beschichtungsanlagen mit hochwertigen Funktionsbeschichtungen ausgestattet werden.
Anwendung finden diese Gläser unter anderem bei Fassaden, die mit nur wenigen Scheiben verkleidet werden sollen, oder auch in verglasten Foyers, die in der Höhe über mehrere Stockwerke reichen. Meistens sieht man solchen mit übergroßen Gläsern ausgestatteten, hochtransparenten Fassaden den planerischen Aufwand der dahintersteckt nicht an. In diesem Zusammenhang bedeuten XXL-Scheiben mehr Weitsicht bei der Umsetzung und eine komplexe Planung. Diese Aufgaben werden bei Interpane von Dirk Sommer, stellvertretender Leiter des Beratungscenters, und Anwendungsingenieur Steffen Schäfer betreut und umgesetzt. Dabei sehen beide, dass der Trend zu solchen beschichteten XXL-Gläsern anhält und sogar weiter zunimmt.
Beispiele für Projekte, wobei solche Gläser zum Einsatz kommen sind beispielsweise „The Shard“ in London, der „Taunusturm“ in Frankfurt sowie der „Apple Campus“ in Cupertino. Diese Gebäude haben die Gemeinsamkeit, dass dort beschichtete Gläser von AGC Interpane verbaut sind.
Bis vor wenigen Jahren wäre dies nicht umsetzbar gewesen, da damals die Sputterkammern in Beschichtungsanlagen übergroße Formate nicht fassen konnten. Heute ist das kein Problem mehr: Interpane Plattling verfügt über einen speziellen Coater, der jede hochwertige Beschichtung auch auf Überformaten bis zu 18 m Länge aufbringen kann. Doch was ist bei der Planung entsprechender Projekte zu beachten?
Ohne eine fundierte Planung geht es nicht
Bei Projekten mit XXL-Gläsern sind die Qualitätsanforderungen an den Gesamtprozess bis zur fertigen Fassade deutlich höher als bei Normalformaten. Sollte im Fertigungsprozess etwas daneben gehen, zum Beispiel beim Vorspannen, bei der Magnetronbeschichtung, der Fertigung der Isolierglaseinheit oder auf der Baustelle im Handling der „unhandlichen“ Formate, ist unter Umständen die gesamte teure XXL-Einheit verloren.
Schon im Planungsprozess werden darum eine Vielzahl an Punkten geklärt, zum Beispiel das Gewicht und die Statik der Einzelscheiben und der späteren Verglasungseinheiten sowie die Statik der gesamten Fassade. Je größer die Glaseinheit, desto mehr Angriffsfläche bietet sie gegenüber den üblichen Lasten.
Das gilt es zu beachten
Die enormen Glasgewichte sind für Standardfassadensysteme in der Regel zu hoch. Um Scheiben in XXL-Dimensionen einzubauen, sind Sonderprofile und –träger notwendig. Verankerungen, Stabilität und auch die Klotzung der ISO-Einheit spielen hier eine wesentliche Rolle.
Das gesamte Gewicht der Verglasungseinheit muss sicher und dauerhaft in der Fassade abgetragen werden. Es müssen zum Teil altbekannte Verglasungsregeln erweitert und auf die großen Einheiten angepasst werden. Gerade bei der Klotzung ist ein erhöhtes planerisches Augenmerk geboten.
Die Auflagerpunkte der Fassade müssen diese Gewichte direkt in die Konstruktion übertragen. Biegen sich hier beispielsweise die Profile zu stark durch, kann das fatale Folgen für die gesamte Fassade haben. Geben die Klötze im eingebauten Zustand nach oder werden nicht die richtigen Klotzsysteme verbaut, kann es im schlimms-ten Fall bis zum Bruch der Gläser führen.
Im Planungsprozess für XXL-Gläser müssen letztlich alle konstruktiven Details geklärt werden, u. a.: Welche Mindestdicken sind in den unterschiedlichen Glasarten wie Floatglas, TVG, ESG, ESG-H einzuhalten und wie wirken sich Veredelungsschritte und zum Beispiel keramischer Digitaldruck aus. Dass Einzelscheiben mit Längen von 18 m hergestellt und beschichtet werden, gewährleistet nicht zwangsläufig, dass auch das Endprodukt in dieser Größe erreicht werden kann.
Deshalb wird von vornherein das Endprodukt geplant, damit geprüft werden kann, ob im gesamten Prozess beziehungsweise den weiteren Veredelungsschritten gegebenenfalls Restriktionen vorliegen, die die gewünschte Größe erschweren. Je nach gefordertem Resultat müssen dann zum Beispiel auch Vorspann- oder Heat-Soak-Öfen, Schleifanlagen etc. vorhanden sein, die auf diese Scheibengrößen vorbereitet sind.
Transport und Montage
Doch damit alleine ist es nicht getan. Die übergroßen Scheiben zu ihrem Bestimmungsort zu transportieren birgt weitere Herausforderungen, ebenso bedarf das Handling und der Umgang mit den schweren Gläsern der Planung. Für den Transport braucht es Spezial-Fahrzeuge. Gleiches gilt auch für die Hebezeuge vor Ort, um die Scheiben sicher einzubauen.
Einer der Interpane-Partner setzt inzwischen Fahrzeuge ein, die bis 21 m lange Gläser sicher aufnehmen und mit mehreren gelenkten Achsen über kurvige Landstraßen fahren können. Geht es nach Übersee, werden die Gläser oftmals mit speziellen Open-Top-Containern verschifft.
Hier sind vorab die Wechselwirkungen der Verpackungen mit Klimalasten und Feuchtigkeit zu kalkulieren. Spezielle Vorrichtungen sind hier nötig, um die Gläser unbeschadet zu verschiffen.
Normale Glasgestelle sind für XXL-Gläser unbrauchbar. Sondergestelle müssen projektspezifisch geplant und gefertigt werden.
Und auf der Baustelle braucht es spezielle Heber und Sauger, mit denen sich diese Sonderformate dann handhaben lassen. Auch bei der Auswahl solcher Spezialwerkzeuge können die Spezialisten von Interpane wichtige Tipps geben.
Teamwork als Basis für den Erfolg
Für den erfolgreichen und reibungslosen Einsatz von übergroßen Gläser für den Fassadenbau müssen vielfältige Faktoren in Planung, Produktion, Transport und auf der Baustelle vorab berücksichtigt und geklärt werden, wobei alle Beiteiligten mit eingebunden sein müssen.
Dieser Prozess funktioniert deshalb auch nur in engster Zusammenarbeit mit dem Glashersteller. Die langjährigen Projekterfahrungen der Anwendungstechniker von AGC Interpane helfen im Prozess von Beginn an entscheidend weiter, von den Anforderungen über die Logistik bis hin zur Baustellenplanung und Montage.—
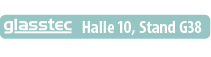