Bereits in der Mitte des 19. Jahrhunderts hatte Henry Bessemer die Idee, flüssiges Zinn als Träger für Flachglas zu verwenden. Im Jahre 1902 erhielt William E. Heal ein Patent in den USA auf das Herstellungsprinzip, Glas kontinuierlich über ein Zinnbad laufen zu lassen und so planparallele Oberflächen zu erhalten. Dieses Patent wurde nie kommerziell genutzt.
Die industrielle Umsetzung revolutioniert den Markt
Alastair Pilkington entwickelte das Verfahren jedoch so weiter, dass es industriell anwendbar wurde, und stellte es am 20. Januar 1959 der Öffentlichkeit vor. 1966 begann die Firma Pilkington Brothers in St. Helens (Großbritannien) mit der Produktion und vergab nachfolgend eine Vielzahl von Lizenzen an andere Flachglashersteller.
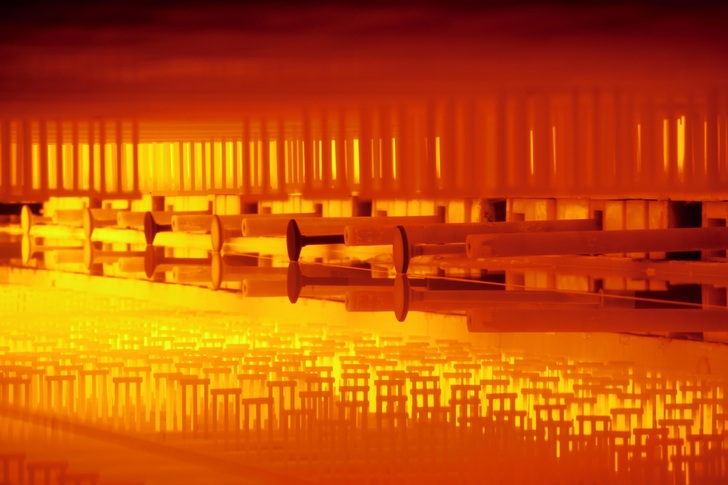
Floatglas ist Flachglas , das im Floatprozess / Floatglasverfahren wird. Hierbei handelt es sich um einen Endlos-Prozess, bei dem die flüssige Glasschmelze kontinuierlich von einer Seite/Richtung auf ein Bad aus flüssigem Zinn geleitet wird. Auf diesem schwimmt (englisch to float) dann das Glas. Mit diesem Verfahren wird inzwischen etwa 95 Prozent des gesamten Flachglases aller Anwendungsbereiche wie Fensterglas, Autoscheiben und Spiegel .
Der Begriff Spiegelglas steht gemäß DIN 1249 (Flachglas im Bauwesen) und DIN 1259 (Glas) für planes und durchsichtiges Glas , wird mittlerweile oft als Synonym für Floatglas verwendet. Da es als Grundlage für Flachglas fast aller Bereiche dient, wird Floatglas häufig auch als Basisglas bezeichnet.
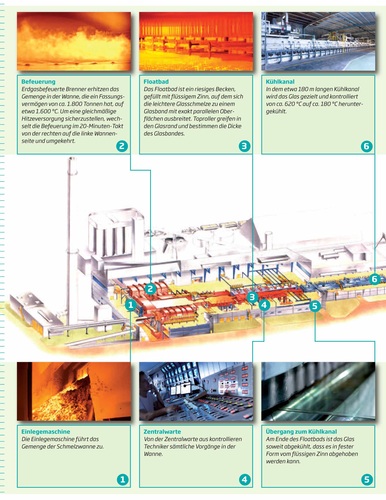
Das auf dem kühleren Ende des Bades erstarrte, immerhin noch rund 600 °C warme Glas wird fortlaufend herausgezogen und durchläuft einen Kühlofen , in dem es verspannungsfrei heruntergekühlt wird. Nach einer optischen Qualitätskontrolle wird das Glas nun geschnitten und als Baisglas an die Verarbeiter und Veredler weiter verschickt. Die Standardgröße einer "rohen" Floatscheibe liegt in Europa bei 6000 × 3210 mm.
Eine Floatglasanlage läuft nonstop für 11 bis 15 Jahre an 365 Tagen rund um die Uhr ( Wannenreise ). Danach ist eine Kaltreparatur erforderlich, bei der die Wannenauskleidung erneuert wird. Zur Veranschaulichung: Eine größere Anlage liefert etwa 3000 m²/h Glas bei 4 mm Glasstärke, was rund 33 t/h entspricht.