Glasexperten mit fundierten Kenntnissen der Automobilindustrie wissen, wie variantenreich und innovativ der Einsatz von zum Beispiel Automobilglas sein kann: Immer geht es dabei um Fahrzeugglaselemente, die dank komplexer Beschichtungsverfahren zu Funktionsgläsern veredelt wurden. Ergebnis einer solchen Veredelung sind dann beispielsweise entspiegelte Gläser, Sonnen- und Wärmeschutzgläser, elektrisch leitfähige Gläser oder gar sich selbstreinigende Scheiben. Automobilhersteller, die sich derartige Scheiben für die Montage ihrer Fahrzeuge zuliefern lassen, arbeiten nach dem Just-in-sequence-Prinzip.
Entsprechend schnell und pünktlich müssen Glasveredeler eine bestimmte Charge ausliefern und zustellen. Denkt man noch einen Schritt weiter, dann ist auch der Glasscheibenhersteller selbst, der die Rohprodukte an den entsprechenden Weiterverarbeiter gibt – ob inhouse oder an eine weitere Firma – an dieser Wertschöpfungskette beteiligt. Nebst Beschaffungs-, Distributions- und Absatzlogistik. „Gerade, weil der Faktor Zeit eine so große Rolle in der Automobilindustrie spielt, kommt ganzheitlich digitalisierten Prozessen bei der Herstellung von Scheiben und Gläsern eine so große Rolle zu. Denn virtuelle Abläufe, die mit der realen Produktion zusammenspielen, sind ein großer Hebel, wenn es um Geschwindigkeit geht“, erklärt Heinz-Josef Lennartz, im Vertical Glass & Solar bei Siemens für Beratungsthemen rund um Digitalisierung, Projekt- und Kundenentwicklung verantwortlich.
Virtueller Produktentstehungsprozess
Bereits im Produktentwicklungsprozess kann die Autoscheibe am Rechner simuliert werden. Entsprechende Produktionsformen können mit wenigen Klicks daraus abgeleitet werden. Die Produktionsmittel und -schritte sind auf diese Weise gleich automatisch virtuell mitentwickelt. Genau diese Abbilder sind es, die man digitale Zwillinge nennt. Doch wer an dieser Stelle den vielgebrauchten Begriff der digitalen Zwillinge bemüht, muss sich im Klaren sein, dass es zu diesem Zeitpunkt noch kein reales Pendant gibt – die Produktion ist zu diesem Zeitpunkt ja noch nicht „in echt“ gestartet.
Stattdessen wird zunächst virtuell entwickelt, getestet und auch gleich schon disponiert. Denn wenn zu einem solchen Zeitpunkt der Auftrag des Automobilherstellers erfolgt, sind die entsprechenden Zulieferer dank virtueller Produktentwicklung und Datenhaltung bereits im Vorteil: Denn die in den weiteren Prozess eingespeisten Daten lassen sich dann so einsetzen, dass die Produktionslinie vorab virtuell in Betrieb genommen werden kann. Diese Simulation erweist sich als großer Vorteil, weil sich dann die tatsächliche Inbetriebnahme der Produktion erheblich beschleunigt. Dasselbe gilt, wenn der entsprechende Scheibenveredeler seinen Prozess auf diese Weise optimiert.
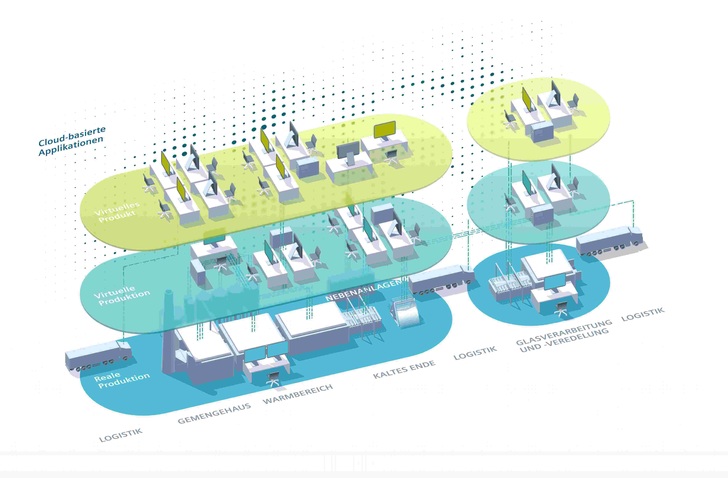
Ganzheitlicher Blick statt Datensilos
Auf den ersten Blick mag dies nach Datensilos klingen. „Doch genau an dieser Stelle setzen wir bei der Vernetzung an. Unser Anspruch ist es, allen Akteuren in der Lieferkette datenbasiertes Arbeiten zu ermöglichen. Doch erst der ganzheitliche Blick auf die Wertschöpfungskette bringt den eigentlichen Mehrwert. Ideal ist, wenn eine einheitliche Datenbasis besteht und die nötigen Infos an den Schnittstellen übergeben werden“, sagt Lennartz. Dass dies keine Einbahnstraße ist, wird spätestens im laufenden Betrieb der Fertigungsanlage deutlich: mögliche Produktänderungen lassen sich erst virtuell durchspielen und dann real anpassen.
Reale Erkenntnisse über Energieverbräuche beispielsweise wiederum werden in die virtuellen Zwillinge zurückgespielt. "Diese geschlossenen Kreisläufe auf Basis einer konsistenten Datenbasis wäre ideal", so Lennartz. Wer dann auch noch eine weitere Vernetzungsdimension in den Fokus rückt, kommt dem Digital Enterprise schon sehr nahe: Dem vertikalen Datenaustausch vom Feld bis möglicherweise in die Cloud. Zum Beispiel können die Qualitätsdaten aus der Produktion in einem IIoT (Industrial Internet of Things)-System wie MindSphere gespeichert und vom Weiterverarbeiter abgerufen werden. Denn dann ließe sich nicht nur Zeit sparen, sondern auch alle relevanten Leistungskennzahlen (Key Performance Indicators) besser erreichen: seien es Qualitätsparameter, Produktivitäts- und Effizienzziele oder auch der Ressourceneinsatz. „Wer weiß, was er will, der kann unglaublich zielgerichtet daraufhin automatisieren und digitalisieren – und damit optimieren“, so Lennartzs Fazit, der von seinen Kunden in der Glasindustrie immer wieder die Bestätigung bekommen hat, dass sie alle auf diese Erfolgsmechanismen „abfahren“ – nicht nur in der Automobilglasproduktion und -veredelung.
Mehr erfahen Sie hier!