_ Der Einsatz von Quality Scannern sollte in erster Instanz für eine konstante visuelle Qualitätssicherung beim Glasverarbeiten sorgen. Ursprünglich erfolgte dies meist in der Mitte des Produktionsprozesses, etwa hinter der Waschmaschine eines Schleif-/Bohrzentrums oder hinter der Waschmaschine einer ISO-Linie.
Das wird zukünftig anders, da neben der Prüfung der visuellen Qualität durch Scanner zusätzliche Aufgaben übernommen werden.
Scanner im Zuschnitt oder davor
Der früheste Zeitpunkt für eine Glas-Qualitätsprüfung ist im Wareneingang oder im Zuschnitt. Eine Prüfung am Anfang der Wertschöpfungskette verhindert, dass fehlerbehaftete Gläser erst nach weiteren Bearbeitungsstufen erkannt, qualitätsbedingt verworfen und vernichtet werden. Gleichzeitig lässt sich mittels Optimierung des Schneidplans die Glasausbeute erhöhen.
Um Rohglas zu kontrollieren, hat Viprotron den Jumbo Controller entwickelt, der im Hellfeldkanal (direkte Durchsicht) Einschlüsse, Blasen und andere Kernfehler detektiert. Optional werden im Reflexionskanal (direkte Reflexion) zusätzlich auch die Schichtfehler erkannt.
Das Prüfgerät ist zwischen Kipp- und Schneidtisch platziert. Da in diesem Bereich Waschmaschinen unüblich sind, unterdrückt der Jumbo Controller über Software-Algorithmen die vorhandenen Lucite-Partikel. Um groben Schmutz oder größere Lucite-Ansammlungen vom Glas zu entfernen, kann eine Gebläse- und Absaugleiste auf der oben liegenden Glasoberfläche eingesetzt werden.
Spezielle Bürsten befreien die untere Glasoberfläche von anhaftendem groben Schmutz. Einzelne Lucite-Partikel, die zur Trennung der abgestapelten Gläser nötig sind, können auf dem Glas verbleiben und werden von der Scannereinheit ignoriert. Diese konzentriert sich stattdessen auf die Kernfehler und/oder prüft die Beschichtung.
Abhängig von der verwendeten PPS Software und der Abstellorganisation nach dem Brechen ist folgender Workflow/Automatisierungsgrad möglich:
- Level 01 - sequenzielles Abstapeln auf Gestelle: Die entdeckten Fehler werden auf einer Brechbildanzeige oder einem separaten Display dem Mitarbeiter am Brechtisch auf dem Schneidplan gezeigt. Sie werden vom Mitarbeiter beim Brechen bewertet und im Falle der Verschrottung kann an der PPS Brechbildanzeige der Nachschnitt angefordert werden.
- Level 02 - Fächerwagen: Die entdeckten Fehler werden der PPS Software gemeldet und diese reoptimiert den ursprünglichen Schneidplan durch Verschieben, Drehen oder Spiegeln von Traveren. Mit dieser Reoptimierung werden Schnitte, Verschnittbereiche oder möglichst kleine Scheiben auf die gefundenen Fehler gelegt. Die Ergebnisse werden auf der PPS Brechbildanzeige dargestellt und der Nachschnitt kann direkt automatisiert werden.
- Level 03 - automatische Zwischenlagerung: Bereits gescannte und im Restplattenspeicher zwischengelagerte Restblätter oder Jumbos werden zukünftig unter Berücksichtigung der Fehlerbilder optimiert
Mit seinem Detect Optimizer kann A+W bereits Lösungen zu allen drei Leveln anbieten. Neben der Vermeidung von Fehlerscheiben und der realen Erhöhung der Glasausbeute, ist der Jumbo Controller ein Instrument zur Bewertung der Basisglaslieferanten. Die Dokumentation der Tests erlaubt Statistiken über Fehlerarten und -häufigkeiten. Damit wird schnell klar, welcher Lieferant die beste oder schlechteste Qualität liefert. Die bessere Rohglasqualität ermöglicht einen besseren Workflow und weniger Nachschnitte.
Kontrollierte Weiterverarbeitung
Die meisten Quality Scanner sind gegenwärtig hinter einer Waschmaschine in der Weiterverarbeitung im Einsatz: in der Bearbeitung etwa hinter einem Schleif-/Bohrzentrum, bei VSG vor dem Reinraum oder beim ISO vor der Visitation. Diese Positionen in der Linie garantieren aus zwei Gründen die besten Detektionsergebnisse:
- Es gibt eine Waschmaschine vor dem Prüfgerät und dadurch ist die Scheibe sauber. Es kommen keine Pseudofehler vor (Staub, Schlieren etc.), die das Ergebnis verfälschen.
- Die zu prüfenden Scheiben sind monolithisch, sodass beim Quality Scanner 3D die vorhandenen Detektionskanäle, die unterschiedliche Beleuchtungen und Betrachtungswinkel simulieren, modular eingesetzt werden können. Monolithisches Glas ermöglicht also den Einsatz von Beleuchtungen und Betrachtungswinkeln von allen Seiten.
Da die Prüfung von gewaschenen monolithischen Scheiben durch den Einsatz unterschiedlicher Detektionskanäle (3D Technik) die beste Fehlererkennung liefert, lassen sich die Systeme hier am effizientesten einsetzen, um die Reklamationsraten deutlich zu senken.
Weiterhin können aus den Prüfergebnissen an diesen Positionen die umfangreichsten Schlüsse für Fehlerursachen gezogen werden. Die Fehlerstatistik erweist sich als gutes Hilfsmittel für die Ursachenanalyse der Fehler, die z. B. durch Handlingfehler auf dem Glas erscheinen. Die gewonnenen Erkenntnisse ermöglichen eine Verbesserung des Workflows im gesamten Betrieb.
Beim VSG oder im ISO kommen zwei oder mehr Gläser im Sandwichverfahren zum Einsatz. Alle Fehler der Einzelscheiben werden letztendlich addiert.
Ein weiterer wichtiger Grund für den Scanner-Einsatz an dieser Stelle ist, dass die Einzelscheiben nach der Fehlerdetektion – speziell von Verschmutzungen – noch ohne großen Aufwand nachbearbeitet werden können. Das ist insbesondere für teure Einzelkomponenten oder für mittlerweile „eilig” gewordene Scheiben sinnvoll.
Endkontrolle wird zum Muss
In der Bauglasbranche ist eine 100 %ige Endkontrolle aller Scheiben bislang nicht üblich. Das kann nach der Novelle der EN 1279 zumindest im Isolierglas bald anders werden. Definierte Produkteigenschaften sollten nachweisbar und nachverfolgbar dokumentiert werden, will man zukünftig teure Reklamationen vermeiden. Dazu gehören die visuellen Beurteilungsrichtlinien, die in der Novelle der EN 1279 I im Annex D den Status „normativ” bekommen.
War der Status bislang „informativ” und somit eine Richtlinie im gutachterlichen Sinn, wird die Norm jetzt das visuelle Qualitäts-Mindestniveau für das Fertigprodukt Isolierglas festlegen. Das gilt auch für die verwendeten Komponenten wie ESG oder VSG.
Weitere mögliche Prüffunktionen
Auch andere Produkteigenschaften, wie der „U-Wert” und damit der Gasfüllgrad (mehr dazu in der Glasrubrik), sollten pro Einheit dokumentiert werden, um später im Rahmen der Eigen- und Fremdüberwachung eine lückenlose Dokumentation der Produktion vorweisen zu können.
Der Quality Checker kann als Kernstück des Qualitäts-Managements hierbei helfen. Schon heute wird die Einhaltung der visuellen Richtlinien mithilfe dieses Prüfgeräts am Fertigprodukt überwacht. Die zum Patent angemeldete telezentrische Beleuchtung hilft, sämtliche von der Norm bestimmten Fehlerbilder an jedem Punkt im sichtbaren Bereich der Scheibe zu detektieren.
Um diese Hauptfunktion herum hat Viprotron weitere Prüffunktionen für die Endkontrolle des Produkts entwickelt, die die Norm oder die Fensterindustrie von den Isolierglasherstellern fordert oder die wichtig für das eigene Qualitätsmanagement sind. Dazu zählen die Prüfung:
- der Elementmaße (Breite x Höhe und Dicke)
- der Glasaufbauten und Abgleich mit dem ERP-System. Dies gilt auch für ähnliche Funktionen bei Sicherheitsgläsern:
- der visuellen Qualität bei satiniertem Glas
- Prüfung der Lochlagen und -durchmesser
- Prüfung der Randausschnitte
Dazu kommt der Abgleich mit dem ERP-System.
Mit diesen Hilfsmitteln wird die Eigenüberwachung deutlich einfacher und die Prozesssicherheit erhöht. Reklamationen und das Garantierisiko werden abnehmen, wodurch der Glasverarbeiter wiederum Kosten reduzieren kann. —
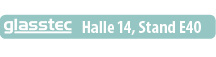